Flash and JavaScript are required for this feature.
Download the video from iTunes U or the Internet Archive.
Description: Professor Gibson takes questions from students in order to review concepts that will be covered on the midterm exam.
Instructor: Lorna Gibson
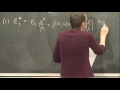
Lecture 10: Exam Review
The following content is provided under a Creative Commons license. Your support will help MIT OpenCourseWare continue to offer high quality educational resources for free. To make a donation or view additional materials from hundreds of MIT courses, visit MIT OpenCourseWare at ocw.mit.edu.
LORNA GIBSON: So I was just going to be here to answer questions.
AUDIENCE: Just clarifying, What was the material that we were covering?
LORNA GIBSON: In the test?
AUDIENCE: Yeah.
LORNA GIBSON: So the test covers everything up to the end of the part on modeling foams, but not the bit on the performance indices, and the material selection charts for foams. So I think up to the end of the fractured toughness of foams.
AUDIENCE: I see. OK. So not covering past [INAUDIBLE].
LORNA GIBSON: Not covering thermal properties, no. It doesn't cover thermal properties. Here you go. So you know I got this MacVicar award, and we had a lunch on Friday at the Catalyst restaurant. And I had to get up and speak. And just as I got up and spoke, there was a red-tailed hawk swooped by the window. It was perfect. It was perfect. Yeah. Hi. So I'm just here to answer questions. So come on. Somebody must have questions. It's all perfectly clear? You want me to do--
AUDIENCE: Talk through test one from last year a little bit.
LORNA GIBSON: You would have to give me test one from last year. I didn't bring it with me. I just brought the problem sets.
AUDIENCE: I have it on my computer, and I could read you the problems or just hand you the laptop. Whichever you prefer.
LORNA GIBSON: Why don't you hand me the laptop and I'll try to do it. Is that OK? OK. So the question is about the test for 2014. OK. So the first question was, describe four processes for making honeycombs, and comment on the type of material usually used for each process. So I did post the solutions, right? Did you look at that?
AUDIENCE: Yeah, I looked at them. I guess I just feel like I don't fully understand why things are there. But I can look at it some more.
LORNA GIBSON: Well, I can go over it, if you want.
AUDIENCE: I'll just look at it some more.
LORNA GIBSON: No, I can go over it. So four processes. Let's see. So there's the expansion process, where you take sheets and you glue the sheets together, and then you pull them apart. So you can only really use that process for materials that are going to have large plastic deformations. So you could use it for metals, some polymers. But you couldn't really use it for ceramics. You couldn't use it for glass because as soon as you yanked on it, you'd break the sheets, right? So--
AUDIENCE: Is it rigid polymers that you can use it for?
LORNA GIBSON: Well, something like nylon you can use it for. Something that's got a little yield, that will have some sort of yield point. Not like if you had epoxy, you couldn't use it for epoxy. So, OK. So that's one process. Another process is a corrugation process where you have a wheel that has little gear knobs on it. And you run your flat sheet through that and it comes out with the half hexagonal profile, and you glue those together. So again, you need something that's going to yield. So that would typically be a metal that you would use that with.
Let's see. Another processor making honeycombs is 3D printing. You can 3D print honeycombs. And there's different ways to do it. One way is by having an ink. So if you want to print in ink, typically that's some sort of polymer that you're printing. I suppose physically it's possible to print glass or to print a metal, but you'd have to have some very high temperature setup to do that. So typically a resin of some sort.
Let's see. Other ways to make honeycombs. You can extrude honeycombs. So the ceramic honeycombs we saw were made by extruding a ceramic slurry. And typically, you would do that with a ceramic that's a slurry and a powder. You wouldn't necessarily do that with a metal. I don't think I've seen any metal honeycombs that are extruded like that. OK?
AUDIENCE: OK.
LORNA GIBSON: Are we good with number one?
AUDIENCE: Yeah, that makes sense.
LORNA GIBSON: We now need your password.
AUDIENCE: Oh, sorry. So is there an actual difference between 3D printing and the extrusion process?
LORNA GIBSON: Yeah. So the extrusion you have a die, and you squeeze the material through the die, right? So extrusion's kind of like the toothpastey thing. And 3D printing, you can have an ink or you can do 3D printing where you have, let's say, a powder. And then you print the binder. And then you heat it up some way to get the binder to cure. And then you get rid of the powder that's not bound. That's another way to do the 3D printing. OK?
AUDIENCE: Can you also pour it into a mold?
LORNA GIBSON: Yeah. Yeah, those silicon rubber honeycombs that I showed you, those are all made by pouring a liquid into a mold and then curing it. Yeah. Yeah, there's other ways, it just asked for four, so I randomly thought of four. OK. OK, are we good? So the next one is a hexagonal titanium alloy honeycomb has h/l is two, theta is 45, and t/l is 0.05. It says, the end constraint factor for elastic buckling is n equals 0.806. The titanium has a modulus of 110 gigapascals, and yield strength of 880. And then you have to calculate some properties. So would you like me to do that?
AUDIENCE: Yeah.
LORNA GIBSON: Yeah, you would? OK.
AUDIENCE: Does anybody else want that?
LORNA GIBSON: I don't see a lot of other people wanting anything else, so I might as well do that. Let's see. I would need a piece of chalk. Here we go. OK. So it's a titanium alloy honeycomb, and we're told h/l is 2, theta's 45, and t/l is 0.05. And we're told that n-- why don't I put the n over here-- n is 0.806. And we're told the modulus of the solid is 110 gigapascals, and the yield strength of the solid is 880 mega pascals.
OK. So it says calculate the value of and describe the mechanism of deformation failure for-- and the first part is the Young's modulus in the two direction, e star 2. OK. So I don't remember these formulas either, so I need to look at my notes. And oh, I don't have the formula for e 2 in my notes. Let me see. Is it in any of the problems?
AUDIENCE: I have the formula sheet.
LORNA GIBSON: You have the formula sheet? I didn't bring the formula sheet with me. You have it? Yeah, I think it's there. I'm pretty sure it's there. OK, so this is just like substituting, and there's nothing complicated about this. So it's equal to Es times t/l cubed times h/l plus sine theta divided by cos cubed theta.
So then you just plug everything in. So this is 110 gigapascals. And I'm going to put 110,000 mega pascals, because it's probably going to be less than a gigapascal. Then t/l is 0.05. So that's 0.05 cubed. And then h/l is 2 plus sign of 45 is 0.707. And then we divide by cos theta cubed, 0.707 cubed. And then I'm not going to work it out, but that's OK. I assume that's what's in the solution. Are we good? So it's just substituting. That's all it is.
In the second part-- OK. You need to change the time on this, because it just keeps timing out.
AUDIENCE: Sorry, I don't know how to change it, but I'll try.
LORNA GIBSON: Oh, is that what this is? OK, this is the test. Oh, this is from 2013. Oh, the next-- if we keep going. Here we go. He's got it, so you take your computer.
AUDIENCE: That's probably better.
LORNA GIBSON: That's perfect for everybody. OK. The second part is the plateau stress for loading in the x2 direction. So that's that. For loading in the x2 direction, it could either be an elastic buckling collapse stress, or a plastic buckling collapse stress. So I'm going to calculate both, and then whichever one is lower, that's the one it would be. So let's see here. So that's going to be-- I'm missing my formulas again. Here we are.
So here's the buckling one. It's n squared pi squared over 24 times t cubed over lh squared times 1 over cos theta. So you put 0.806 squared in here. Pi squared 24. So here you go. This is t over l cubed times h over l squared. So that would be 0.05 cubed. And that would be 1 over 2 squared, and then 1 over 0.707, and then whatever that equals. OK? Are we good with that? And then you'd want to calculate sigma star to plastic. And that's equal to sigma ys, t over l squared, and 1 over 2 cos squared theta. All right?
So then sigma ys was 880 mega pascals. And t over l was our 0.05. And that's 1 over 2 times 0.707 squared, and then whatever that equals. OK? And then whichever one of those would be less is the plateau stress. So I don't-- yeah?
AUDIENCE: So I know-- I think I made this mistake in the problem set, but here, because it's titanium, we don't consider it brittle.
LORNA GIBSON: Right. Right. I mean, you could. But you don't need to.
AUDIENCE: That was something with ceramics?
LORNA GIBSON: Yeah, or if it was a glass, or ceramic, or maybe an epoxy. Something that was brittle. And besides which, if you look at the question, I only give you a yield strength and a solid modulus. So to get the brittle thing, I would have to give you a fracture strength.
AUDIENCE: That's true with all the problems.
LORNA GIBSON: I usually give you what you need. Especially on the test, I'm going to give you what you need. You're not going to be looking things up. OK? So we're good so far? OK, let me go back to the question. So then the third one is the out of plane Young's modulus in the x3 direction. And that's just going to be Es times the relative density. And the relative density-- let's see. So it's Es times rho star over rho s. So that's 110,000 mega pascals. And then there's also the very first equation on this is the relative density. So it's t/l times h/l plus 2 divided by 2 cos theta h/l plus sine theta. So I'm not going to substitute everything in, OK?
So that was it. It was very plug and chug. Are you good?
AUDIENCE: Can I ask a question about a specific question.
LORNA GIBSON: I'm going to go through the rest of them. She wants me to do the whole test. You want me to do the whole test, right?
AUDIENCE: That would be great, but if other people have other questions it's fine.
LORNA GIBSON: Why don't I do the whole test. And then there's going to be time, I think.
AUDIENCE: [INAUDIBLE].
LORNA GIBSON: Let me do the test from last unit. OK, so that's number one. Or that's one and two. And then three is, a closed cell elastomeric polyethylene foam has a relative density of 0.05 and a volume fraction of solid in the edges of 0.6. They give you the Young's modulus of the solid is 0.2 gigapascals. The pressure within the cell walls is atmospheric, 0.1 mega pascals. And the Poisson's ratio of the foam is 0.3. And you're asked to get the Young's modulus of the foam, the compressive plateau stress. And then there's a question about why does the Young's modulus depend on the solid modulus and relative density, while the Poisson's ratio does not.
So let me go through, then. So the first one is, what's e star. And we're told relative density is 0.05. The volume fraction in the edges is 0.6. So remember, that was what we called phi. So phi's 0.6. The Young's modulus of the solid is 0.2 gigapascals. The initial pressure within the cells is 0.1 mega pascal. and Poisson's ratio for the foam is 0.3. And it's a closed cell.
So if you remember-- oh, let's see. I think back here, was I supposed to-- I was supposed to say something about the mechanism of deformation and failure for the first one. So the mechanism of deformation in the modulus in the 2 direction is bending. The mechanism of failure here is buckling. The mechanism of failure here is yielding. And the mechanism of deformation here was axial deformation, OK? So I forgot to say that.
OK, let me go back here. So for this one, if it's a closed cell foam, remember there were three terms to the modulus. There was one from bending of the edges, one from stretching of the faces, and one from the gas contribution if you've got gas inside the cells. So again, I'm going to have to peek at the equation. Foams. Here we go, foams. OK. And then this gas one. Get rid of that. OK, so this one is just the same kind of thing. It's just plug and chug. Do I need to put all the numbers in?
AUDIENCE: No. I guess I'm a little bit confused why you need the pressure term. Because you talked about faces bursting.
LORNA GIBSON: Ah, so if it's the modulus, remember the modulus-- so the question is, why do you need to worry about the pressure because I talked about the faces bursting. And remember, the stress strain curve looks something like that. Maybe the slope of the curve is a little bit higher over here. But this is the modulus down here, right? The modulus is related to the initial stress strain relationship. And initially, they're not going to burst. You'd have to load it up to some amount of stress before the faces burst, right?
So when you're down here, the faces certainly down at the beginning, they're not burst, right? You have to get some stress before they're going to burst. And in some materials, when you get up around here, around the plateau stress-- let's just call that sigma star-- then they might burst. And then the pressure term would disappear and the face term would disappear. So if I don't tell you to ignore them, if I don't say they're going to burst, or I don't say they're negligible, I would calculate them. And then if they're small, then you say, well, they're negligible. OK? Are we good with that? You're good? You're good? Sardar, you don't need to be here. But you can stay if you want, but you don't need to be here. OK, are you good? Everybody else good? OK.
That was A. B, what's the compressive plateau stress of the foam. So here, they want to know what sigma star is. You're told it's elastomeric. So if it's elastomeric, it's like a rubber. It's rubbery. So if it's rubbery, it's going to buckle. It's not going to yield. It's not going to be brittle. So you can just calculate the elastic stress here. And if we flip over to our handy dandy list of equations-- blah, blah, blah, blah. Oh, pooh. I'm realizing-- yeah, so I don't have the term here for the faces or for the gas, so here we could assume it's going to rupture. So let's assume it's going to rupture.
So if we assume that it's going to rupture, it would be just like the open celled foams. And then you can just use that. And that's been found to work fairly well for the open celled and the closed cell foams.
AUDIENCE: And we assume that faces rupture because--
LORNA GIBSON: Well, to be honest, I can't remember if last year I got to this point in the test and somebody said, we don't have the equation, and I gave them the equation with the other terms, or if we just assumed that the faces ruptured. I can't remember. To be honest, I think probably for elastomeric foam, you could assume that they'd probably don't rupture unless they're very, very thin.
AUDIENCE: So what kind of foams do they typically rupture in?
LORNA GIBSON: So certainly if you had a metal foam, they'd probably rupture. If you had, say, a polymer foam that was more rigid, like a rigid polyurethane. So polyurethanes can be flexible, which means they're made out of an elastomer, or they can be rigid. And the foams that are typically used for insulation, thermal insulation, are typically closed celled polyurethane foams. And those typically have very thin faces, and they would rupture. Yeah?
AUDIENCE: Are you looking for the Young's modulus in this problem?
LORNA GIBSON: The Young's modulus was the first part, right? So part A was the Young's modulus.
AUDIENCE: In B--
LORNA GIBSON: In B is the collapse stress, the compressor strength.
AUDIENCE: So I think in my notes, I think it has this. If the--
LORNA GIBSON: Right, if p0 is bigger than-- so what she's showing me in her notes is I had a little note in the class, in the lecture, that if the initial pressure in the cells is greater than atmospheric, then the cell walls are pre-stressed and you have to overcome that in the buckling.
AUDIENCE: Is that atmospheric?
LORNA GIBSON: That is atmospheric pressure.
AUDIENCE: So you don't need the [INAUDIBLE].
LORNA GIBSON: No. Yeah. OK? OK. Yeah, you don't know that that's atmospheric. So do you ever do things in PSI? No, you don't. Because when I was a student a long time ago, the thing I remember learning was atmospheric pressure is 14.7 PSI, more or less. And the conversion between mega pascals and PSI is there's more or less 145 PSI to a mega pascal, so the atmospheric pressure is about 0.1 mega pascals. Yeah?
AUDIENCE: I don't know if this is a silly question, but for part B, how do we get from the Young's modulus of the foam--
LORNA GIBSON: Oh, sorry, sorry, sorry, sorry. I put the wrong thing down here. Sorry, my mistake. OK, now you happy? Sorry. OK, shall I move on to the next part? Another question?
AUDIENCE: Well, I had a question about number two, but maybe we can come back to that--
LORNA GIBSON: OK, let me finish this, and then we'll go back to number two. So this one here, the part C is why does the Young's modulus foam depend on the solid modulus and the relative density while the Poisson's ratio does not. So when I write the equation for the Young's modulus, the solid modulus comes into it, the relative density comes into it. And remember when we had the Poisson's ratio, it's just a constant that depends on the cell geometry. So here's C, nu star just as a constant. And that constant just depends on the cell geometry.
So if you think of the Poisson's ratio, it's the ratio of two strains, right? So say I have my foam here. So say that's just a block of foam. Little cells in it here. Little cells. And say I press on it this way here. And let's call this the one direction and the two direction. If I press it in the two direction, the Poisson's ratio is then just nu would be-- let's see, this would be 2, 1. It'd be the strain in the one direction over the strain in the two direction. So it's the ratio of two strains, right?
And if you think of our model for the elastic behavior of the foam, each of those strains is going to be related to some bending deformation in the cell walls or the cell struts. And this strain here is going to be-- let me make this proportional. It's going to be proportional to a delta over l. And this one here is going to be proportional to the delta over l. So this might be delta in the one direction, and this will be delta in the two direction. But those two things are both going to be related to the bending deflection of the beams, right?
And since both of those deltas are related to the bending deflection of the beams, we could write them-- if you want, I could write that as f l cubed over E of the solid times t to the fourth. And then that's times 1 over l. And then this thing here is also f l cubed over E of the solid t to the fourth 1 over l. So everything cancels out except the geometrical constant. And if you remember when we did the honeycombs, it looked exactly the same.
When we looked at the Poisson's ratio of the honeycombs, we had the strain in one direction over the strain in another direction. And each of those strains was related to some component of delta. There was a delta 1 and a delta 2. But the delta 1 might be delta sine theta and delta 2 was delta cos theta. So if the deltas are the same, then it all just cancels out. And all you're left with is a geometrical constant. OK? Do you get physically why that is?
AUDIENCE: So I have a question about this. Because we're given most of the equations that we need, is it only in conceptual questions that we should know how we actually derived that version?
LORNA GIBSON: I'm not going to ask you to derive that equation for a closed cell foam.
AUDIENCE: I meant this last part.
LORNA GIBSON: Well yeah, you should be able to explain that. But I mean just at this level. Nothing very mathematically involved.
AUDIENCE: OK, cool.
LORNA GIBSON: OK, are we good? So that was the end of the test for the undergraduates, OK? And then for the graduate students, just like the problem sets, I just have an extra question. And that's what I did this year, too. So the graduate students have one extra question. So you and you. Is anybody else a graduate student? I think it's just the two of you. You're post post-graduate. OK. OK. So let's see.
So this one says, the performance-- so this is on the performance indices which I told you you didn't need to know for this test, partly because, remember, we missed two lectures. We're not exactly on the same spot as we were last year. But I can do it if you want. Do you want me to do it, or should we do other questions?
AUDIENCE: What do the grad students think?
LORNA GIBSON: Sure. OK. So the question is, the performance index to minimize the mass of a beam of a given bending stiffness, length and square cross-section is e to the one half over rho. So you remember, we derived that e to the one half over rho in class. In the section on wood, we saw that this performance index for wood is higher than that for the solid cell wall material in wood. Do you remember that? The e to the one half over rho for the wood was, I think, rho s over rho star to the one half times Es to the one half over rho s.
So explain why wood has a higher value of e to the one half over rho than the solid cell wall material. And then part B is, suggest a design for an engineering material based on wood that has high values of e to the one half over rho. So one way to explain it is to say that if you're looking at e to the one half over rho, you can say for wood, E over Es is equal to rho star over rho s for loading in the axial direction. So this will be for loading actually along the grain. And that's what we were looking at. So that's what I'm talking about here.
So I think-- let me just see if this is right. Yeah. So this equation here is exactly the same as that equation there, right? And this is basically saying that this is the performance index for the wood. This is the performance index for the solid. And this factor here is bigger than 1, because the solid density is higher than the wood density. OK? So really, all you have to do is say that for the wood, the modulus in the longitudinal or the axial direction along with grain varies linearly with the relative density. And it probably would be a good idea to say that this is a result of the cell walls deforming axially.
So when you take the cells, if you think of the wood cells as being something like that and you're loading it this way on, the cells just actually shorten, and the modulus depends on the-- it just is the volume fraction of solid times the modulus of the solid. And that's where this comes from. And once you have this, that basically gives you that. OK? Are we good with that? So that's why it's higher.
Another way to look at it as sort of more of a hand-wavy argument is that if you have a certain amount of solid-- so say you have a certain mass of solid. If it's solid, it takes up a certain cross-sectional area. So say that your beam's a certain length, that's going to have a certain cross-sectional area. And if you have wood, if you have a cellular material, if you have the same mass, you're essentially making the dimensions of that piece bigger. So you're moving the material further away. And as you're making it bigger, you're increasing the moment of inertia. And so you're increasing the bending resistance of it. That's another, more hand-waving way to talk about it.
And then the second part is to suggest a design for an engineering material based on wood that would have high values of e to the one half over rho. So remember when we looked at those material performance charts, we said that wood was similar to engineering fiber composites. But those data for fiber composites are assuming that it's solid, the fiber composite's a solid. So if you could take fiber composites and make little tubes of fiber composites and assemble the tubes together so that it was like wood, would get something that would be even higher.
So if you could make, say, a fiber composite honeycomb material, and you'd want to have the fibers aligned along the prism axis of the honeycomb, then you would get higher values. It would be the same-- it'd be this sort of argument again, but now with a fiber composite. So you'd want-- if this was your fiber composite like this, you'd want the fibers-- well, in wood, they're at a little bit of an angle. But say they were lined up like that. You'd want them something like that, then loading it that way on, right?
And if one way to think about those charts is if you-- say we had a plot. And say this was log of the modulus and that was log of the density. And I think I'll just draw the envelope. So foams were somewhere down here, metals were somewhere over here, and with elastomers we're somewhere in here. I think ceramics were up here. And then I can't remember exactly where composites were, but composites were around about here. I'll just say FRC for fiber reinforced composites. And I think woods were kind of in here. Something like that.
And then we had our performance index, right? So remember, there was a performance index, something like that. And that slope of that was e to the one half over rho. So every point on that line had the same value of e to the one half over rho. And essentially, if you had the fiber composite and you made a honeycomb out of it, you would be taking the data from here and shifting them out that way. You'd be pushing them out over here, so you'd get a higher value of that performance index. OK? So that's the test from last year. That's the end-- yeah?
AUDIENCE: So for along right here or different it would be cubed.
LORNA GIBSON: Yeah, so the thing about the honeycombs is--
AUDIENCE: The opposite.
LORNA GIBSON: Right.
AUDIENCE: [INAUDIBLE].
LORNA GIBSON: It'd be worse, that's true. So the thing about the honeycombs is they're very stiff in the axial direction, but you pay for that in the other directions. And it's the same for wood. So the wood is very good when you load it along the grain, but you pay for it the other way. But if you think of from the tree's point of view-- if you're a tree. So here's my little tree. So here, say we have a tree trunk, and we have some branch. Branch over here, branches, tree. So the grain is lined up this way. And then when there's a branch, the grain turns around and goes that way, right? So if you think of the tree as a whole, the whole tree blows in the wind like this.
So it's like a column like this, and everything's lined up that way. And you're loading it this way. So that is the stiff direction, right? And if you're a branch, the branches are more loaded by gravity. So they're loaded that way. And then because the fibers, the grain turns around, they're also oriented in the good direction. So from the tree's point of view, it's optimized things.
Then you remember when I talked about the old wooden sailing ships, when they made the old wooden sailing ships, if this was the deck here and that was the haul there, they would get pieces of wood to fit in here that were called the knees. That was the knee. And they would try to get a piece that was from a branch like this. And they would try to match the curve of that joint with the branch with the curve that they needed in here so that the grain followed the pattern of what they needed for the boat. OK. Other questions?
AUDIENCE: I'm not quite sure what the difference between tangential versus ray here.
LORNA GIBSON: Oh, OK. So in the wood, you mean?
AUDIENCE: Yes.
LORNA GIBSON: OK. So can I rub this stuff off? We're happy? Let's see. Say again? So tangential and radial. OK. So say the wood cells look something like this. So these would be the fiber cells or the tracheids And then the rays typically are more rectangular cells. So they might look something like that. And then they would be some more fibers or tracheids, depending on if it was a soft wood or a hardwood. So these would be either fibers or tracheids in a hardwood or a soft wood. And then these would be the ray cells in here. So they have a different structure. They just look different. They're different shape.
AUDIENCE: This is the top? From the top?
LORNA GIBSON: Yeah, this is looking from the top down. And then if you think of the tree-- so the tree's going to have growth rings, right? So the growth rings are going to look-- obviously I'm not making perfect circles, but you get the idea-- something like that. And then the rays go this way. They go radially. OK? So this would be the radial direction, and then those are the rays. Are we good?
AUDIENCE: So which way's the tangential?
LORNA GIBSON: So the tangential would be this way on, OK? So if I loaded this way like that, that would be loading it in the tangential direction. And if I loaded it this way, that would be loading it in the radial direction. The length of the rays runs in the radial direction. The length this way on. So this thing here corresponds to one of these lines I've drawn here. And then these guys here are the stuff in between here.
AUDIENCE: How do you know what the tangential, the Young's modulus and stiffness is?
LORNA GIBSON: So say we were loading it tangentially, we're loading it like that. Then--
AUDIENCE: If you have a tree, how do you apply a tangential load on it?
LORNA GIBSON: Oh, well it's not the whole tree, right? So say we have a piece of wood that we cut out like this. So say I have that. And if I loaded it this way on, I'd be loading it tangentially. The tree's big, right? So I'm not talking about loading the whole tree, I'm talking about taking a piece of wood out of the tree and loading it.
AUDIENCE: OK, so you can't really load tangentially for the entire trunk.
LORNA GIBSON: No, I'm talking about taking a piece out and loading that piece.
AUDIENCE: How about a ray here? Do you take the--
LORNA GIBSON: So the same thing. You'd take-- say this was the piece of wood that you were looking at. Now you would just load it this way on. OK? I think-- I brought my thing because I have the slides. Let me see if I can find-- I think there was a slide that showed this. OK. That was Furry Fridays. That was the wood sculptor. Here we go.
OK, so imagine that that cube is your piece of wood that you're loading, right? So imagine this is the-- you cut a little piece out. Then you're loading it tangent. Can you see, then? You can load it-- you're not loading the whole tree.
AUDIENCE: Yeah, I was thinking about loading the entire tree and then applying the tangential load on it.
LORNA GIBSON: Yeah, because then-- I see the problem.
AUDIENCE: It's going to give us shears.
LORNA GIBSON: Yeah. Yeah, because I could say, well, if I was trying to load the whole thing. Say I was loading it from here to there. Well if you look at it one way, it looks tangential. If you look at it the other way, it looks radial. So think of cutting a piece out, because that is what you're going to do. You're going to cut a piece out. OK? All right. Are there other questions? Yes?
AUDIENCE: With that formula sheet, do you only give that formula for the honeycombs, or also for the foams?
LORNA GIBSON: I'm going to give you-- if you look at, I think, problem set 2, I gave you a sheet that had three pages of equations. And it looked exactly like this. So there was one saying, properties of two dimensional cellular solids-- honeycombs. There was a whole thing of in plane properties and out of plane properties. That was one page. The next page was properties of regular hexagonal honeycombs. And then the next page was properties of three dimensional cellular solids foams.
AUDIENCE: OK, excellent. Thank you.
LORNA GIBSON: OK? Like I just said, I think there's maybe one or two equations missing from this. But if it was something you needed, I would give it to you. I would give it to you. OK?
AUDIENCE: So I should have scrolled down for it?
LORNA GIBSON: What? You should have scrolled? So you're like me. This happens to me all the time. I have some website. I'm looking at it. I'm like, OK. I got it. I think I've got everything. And then I realized I'm supposed to-- I missed something because I was supposed to scroll down.
AUDIENCE: Problem set two was only the honeycombs. That's why.
LORNA GIBSON: Well, I think that was probably all we covered was the honeycombs on that problem set.
AUDIENCE: So that's why I only got that part.
LORNA GIBSON: OK. All right, yeah. So I'm going to give you, this will be attached to the test. OK? So I think on the test that I posted it was attached, wasn't it? Yeah. [INAUDIBLE], did you have a question?
AUDIENCE: For 2 part D, I don't think we went over that. I was confused as to how-- is it just that equilateral triangular cells always have-- is always truss behavior?
LORNA GIBSON: Let's see.
AUDIENCE: Oh, sorry. It's the 2014 test.
LORNA GIBSON: 2014-- oh, sorry. I missed a part. Sorry. Yeah, so it says, the same titanium alloy is used to make a honeycomb with equilateral triangular cells. And what is the in plane Young's modulus for loading in the x 2 direction of the triangular honeycomb? So this is-- say you have cells that look like that now. And that's x 1. That's x 2. OK. So the Young's modulus for this-- so I happen to remember the formula. So I guess I'm thinking you might have put this on your cheat sheets. It's 1.15 times Es times that, times the relative density. So I'm trying to remember. Do I have that on here? I don't have it on here.
AUDIENCE: Are we just supposed to know that? Are we just supposed to--
LORNA GIBSON: Well, I guess what I would hope that you would know is maybe not the constant, but that it should go as Es and linearly with the relative density. Because it's a truss and because it deforms axially. I don't really expect that you would remember the 1.15. Yeah?
AUDIENCE: So does that mean for all the foams, of which there were like 10 constants, we don't need to write all down, like what C1 equals--
LORNA GIBSON: I think that's what this thing gives you. Let's see. It gives you all the Cs. All right, then I'll make sure I give you the Cs. I'll make sure I give you the Cs. But who's got a pen so I can write that down to make sure that I do that? Does somebody got a piece of paper. Or I could write it down here. Oh, here we go. I can write it down this little sticky thing here.
OK. So I'll stick that on there so I remember to do that.
AUDIENCE: Will you also be writing what Cs? Because you have, in your equation, C1, C2--
LORNA GIBSON: Well, I think I would say-- say I asked you for, I don't know, the yield stress for a foam in compression that yields plastically. I would say, the constant for that is 0.3. I wouldn't give you C2. I wouldn't do it by numbers, I would tell you what the number was for the thing you needed, because I mean the way the numbers are, the only reason they're numbered is because that's the number they are in the book. They're just ordered sequentially in the book. But I don't expect you to remember which-- it's C6, or C5 or something. So anyone else?
AUDIENCE: Can you explain the difference between uniaxial yield and plastic buckling?
LORNA GIBSON: Oh, OK. So if you have something and it fails by uniaxial yield-- so say you have a honeycomb like this, and you're loading it this way on, OK? So if you're loading it that way on, these walls of the honeycomb are just axially deforming, initially. Right? So the elastic behaviors, they just axially deform. So it works out that if these cell walls are very thick, then you can reach a yield stress before any buckling occurs. And then the strength would just be that yield stress of the cell wall material times the relative density. OK? But the cell walls have to be thick for that to happen.
So then imagine that the cell walls aren't thick. Imagine that the cell walls are thin. So say I have the same honeycomb like this. If the walls are thin, and say the solid material itself-- so this is for the solid-- it has some stress strain curve. And it may have a linear elastic part, and then a yield thing like that. So say this is the yield strength here. Say we compress that this way on the same thing in the three direction. Then if a material's got a yield point, there can be an interaction between plastic yielding and elastic buckling. And you can get plastic buckling.
And the plastic buckling, you're going to get the wrinkles that go along the length of it this way. remember I showed you that tube that kind of collapsed and folded up kind of thing? That's plastic buckling. OK? And typically, people use what's called the tangential modulus to calculate the buckling stress for plastic buckling. And the tangential modulus would be something related to the tangent over there. I don't expect you to be able to derive plastic buckling equations. But the plastic buckling-- you know what elastic buckling is, right? Yeah. Yeah.
So one way to think about plastic buckling is, if you have-- and I'm trying to remember. This is called the slenderness ratio. And I'm trying to remember, is that l over r? Imagine you had just a circular cross section and you had a length, l. So you have a column here, and it's got a length, l, and it's got a radius, r. Like that, OK? So the longer it gets, the more slender it is, the higher the slenderness ratio is. And this, I think, is some sort of stress.
If the slenderness ratio of just a single column is short-- if it's stubby, if you had a column that looked kind of like that, It's not going to buckle. It's going to yield. And so if you compress that, it would just yield. And it's just going to yield at the yield stress, right? It's just going to yield at sigma y of the solid, whatever the solid is. If you have a long column, it would buckle elastically by an Euler buckling. And Euler buckling-- let's see. I'm going to run out of room here.
If you think of it in terms of a stress instead of a load, it's going to be in squared pi squared Es i. Let's say i goes as r to the fourth. And this is going to be l squared r squared. Right? This is going to be a pi in here. There's going to be a pie in here. I might have lost a factor of 4, but it's going to be-- let me make this proportional, OK?
So the slenderness ratio, there's going to be an l over r squared term here. So I could cancel out the four there and put a squared. So sigma Euler is going to go as Es times r over l squared. Like that. And so this is the Euler buckling stress here, OK? So this would be elastic. And right here at this little corner, it turns out life isn't quite that mathematically exact. If you're near that corner, it's not like here it's buckling elastically, and here, it's buckling plastically. What happens is, if you looked at data, data might do something like that. So the sum interaction between the elastic and the plastic. And that's kind of what's going on with this thing here. Does that makes sense?
AUDIENCE: Plastic buckling can-- OK, so if you unload plastic buckling, you get some of the elastic part back?
LORNA GIBSON: You're not going to get much back.
AUDIENCE: You're not?
LORNA GIBSON: No, because once-- to get the plastic buckling, you're very close to this. By the time you get that deformation, you've got locally, it's yielded. It's not all elastic everywhere. It's going to yield in places. And once it starts yielding, it's-- if you think of these buckles forming, it's not like you're at one spot on this curve throughout the whole thing. Some of it's more deformed, and some of it's less deformed. Let me pull up those plastically buckled columns, those tubes. Get rid of that one. Let me try and remind myself where they were. I think-- honeycombs, I want honeycombs. Out of plane, that's what I want. It was this thing here.
So you see when you have-- that's just one tube, but the whole honeycomb would-- imagine that you have groups of tubes put together. They would have to fail in some compatible way. But the deformation and the stresses are not going to be uniform through this whole thing, right? One part of it's going to be at one stress, and something else is going to be at another stress. So parts of it are going to yield plastically, and you're not going to recover that. OK? So in fact, they use these sorts of things for energy absorption devices, like in cars and things like that. To absorb the energy from the impact. More questions? Let him have a turn.
AUDIENCE: Sorry, I have a question about I think 2013.
LORNA GIBSON: 2013, OK.
AUDIENCE: The last question. It's about the plastic.
LORNA GIBSON: 2013. Let me rub some of this stuff off. OK. Here we go. OK. Oh, we haven't covered this at all. So the last question, this one here?
AUDIENCE: Right.
LORNA GIBSON: Yeah, so this question's on energy absorption. We haven't got there yet.
AUDIENCE: How about-- OK.
LORNA GIBSON: And the third question's on sandwich structure. So when I taught the course in 2013, I did the topics in a different order. So I did honeycombs, and I did foams. And then I think I did sandwich panels, and I did energy absorption. And I left the stuff on the wood and the cork to the end. So we haven't done that. So don't panic if you haven't-- if you can't do that. OK? You should have known. Come on, you should have known that if it talked about things we haven't covered yet, I'm not going to give it on the test. OK, what else?
AUDIENCE: Can you explain more plastic hinges?
LORNA GIBSON: Plastic hinge, OK. So let's just say we have a beam in bending, OK? And say it just has a load p in the middle, all right? Are we good? So this load in the middle, then this reaction is p over 2, and that reaction is p over 2. And if I drew the sheer force diagram, it'd go p over 2 up, we go over, go p over 2 down, like 2 p over 2 down. Over and back up. OK? And then if I drew the bending moment diagram, it would go up and down like that. And that would be zero. And that would be zero. And this would be PL over 4. OK? Are we OK with that? We haven't got to the end of the answer, but--
AUDIENCE: I have a question. We're not expected to--
LORNA GIBSON: No, no, you don't need to do this. I'm just trying to explain it now. You don't need to retain that information, for heaven's sakes. No. Come on, I'm so disappointed.
AUDIENCE: For the moment, is it positive for the counterclockwise turns?
LORNA GIBSON: Oh, so you remember for the beam bending, there's a different convention. It's positive if it's tension on the bottom. Are you in mechanical engineering? I though you were in mechanical engineering.
AUDIENCE: No, I take physics.
LORNA GIBSON: Oh, you do physics. All I really want to say is the moment's maximum in the middle, OK? So let me just say the moment's maximum in the middle, OK? So then let's look at the cross section. So say I look at a cross section here. Let's just make it rectangular to make it easy for me to draw. So it has width, b, and a height, h. OK? So this would be h on this picture over here. And remember, the neutral axis goes through the middle on the cross-section here. And so one half of the beam is in tension, and the other half of the beam is in compression.
So for this situation here, this half of the bean is going to see compression, and that half of the beam is going to see tension, OK? Are we happy with that? We're happy with that. OK. Now let me draw the stress distribution. So if it's linear elastic and it hasn't yielded yet, the stress distribution is going to look like this.
So this is h again. That's the height. And now b is into the board. And I'm plotting the stress this way. So this thing here is my neutral axis. It has no stress. Remember, there was one plane that has no stress, and for a rectangular cross-section, it goes through the middle of the cross-section. It goes through the centroid. Is this ringing a bell? I'm hoping this is ringing a bell. Come on. I know we did this in 302, too. I know we did. OK.
OK, so this is all linear elastic, right? So at some point-- so I'm going to get to the plastic hinge. At some point, If you keep loading it and p gets bigger and bigger, the moment gets bigger and bigger, the stress gets bigger and bigger remember, the equation here for the stress is equal to My over i. This moment, the maximum moment's going to be this moment here. The maximum y is going to be h over 2, the distance from the neutral axis. And i is going to be bh cubed over 12 for the rectangular section.
So if I keep loading it up, at some point, the maximum stress is going to equal the yield stress. right? And in our cellular things, is going to equal the yield stress of the solid. So our beam is one of our edges in the foam, or struts in the honeycomb. So at some point, is going to equal the yield strength of the solid. So let me draw the stress distribution again, where we start to have plasticity. So here, the stress is equal the yield stress. And it's going to equal the yield stress at the bottom, too, because it's all symmetric, right? And the neutral axis is still going to be in the middle here. So it's going to 0 down there.
So initially, when it's just barely reached the yield stress at the outer part of the beam, then this stress distribution would still be linear in between. But once you start to load it more than that, then the plastic region starts to seep in from the outside inwards. And what we do here is we assume that the solid is elastic perfectly plastic. And if you remember, when we said things were perfectly plastic, or if they were elastic perfectly plastic, they look like that. The stress strain curve for the solid, I'm assuming, looks like that. So I'm assuming the yield stress in the solid is just a constant. That if I strain it more, there's no work hardening. I'm neglecting work hardening.
AUDIENCE: You said inward that the--
LORNA GIBSON: In board?
AUDIENCE: Inward, you said something like--
LORNA GIBSON: Inward. So this is-- let's see. I didn't bring a bean with me today. No beam. Do we have anything beam-like? Ah, here we have a beam-like thing. OK. So say this is my beam, and I'm loading it this way on, OK? And this is b, and that's h. So this picture here is looking at it that way on, OK? And this picture here, I've drawn h, but now I'm just looking at the stress distribution across h. And b is into the board. Is that OK? Does that answer your question?
AUDIENCE: No, I mean for the plastic.
LORNA GIBSON: For this part? OK. I'm working up. I haven't finished it yet. So this is the same kind of view as here. I drew it a little bigger. It shouldn't have draw bigger, I should have drawn it the same height. But it's the same thing. OK? So you'll buy that at some point, we reach the yield strength here. And if I keep loading it up and I assume that the solid is perfectly plastic, that there's no work hardening, then the stress distribution would look like this. OK? And then if it yields more, then it's going to look like that. And if it yields more, eventually I'm going to get to the stage here, where it's-- let me redraw this. That would be-- you get the idea, OK? This will go over here, and down here, and like that. OK? OK.
So are we happy with this stress distribution across the cross-section? Yeah, OK. So that's when it forms the plastic hinge. So when it forms a plastic hinge, the stress distribution looks like this. So these are supposed to be the same size. They're not quite. Let's see. So one of the things I talked about was the plastic moment that kind of characterized that plastic hinge. And the plastic moment is just the internal amount of moment that the beam can withstand when it's yielded completely across the whole cross-section. So when we're at this point here.
So you calculate that by saying, that stress there is equivalent to a force. That stress there is equivalent to a force. And you get the moment by multiplying those forces times that distance there. OK? Because you think of those two forces as being a couple, and the moments the force times the distance between them. So the plastic moment was sigma ys. And say we're talking about our honeycomb or foam or something. That was our cell wall thickness t. So let me call it t instead of h for the foams and the honeycombs.
So this force here is going to be the stress time the area over which it acts. And let's say we look at it for a honeycomb. Then I've got the stress is acting over this distance here, and then times the depth into the page, right? And if it's the honeycomb, that depth into the page is just b, OK? And then this moment arm here is just t over 2 as well, because that's t over 4, and that's t over 4. So it's t over 2 again. So it's sigma ys bt squared over 4 for the honeycomb. And say we have an open cell foam. The edges aren't of thickness b, they're of thickness t. So then it's m p is just sigma ys t cubed over 4.
Are we happy? And really, physically what that is is it means that the beam can't hold any more force. You can't apply any more force to it. It's just going to rotate like this once you've gotten to that plastic moment. That's why it's called a hinge, because it just can rotate like hinge rotates. Like a door hinge, OK?
AUDIENCE: How does it rotate?
LORNA GIBSON: Well, where's my original picture. So if this was the beam, when you form the plastic hinge, your beam would just look like that. And this would be your hinge point. I'm a civil engineer originally. We try to avoid this. So that's why, in the foam and in the honeycomb, that's when it fails is when you get that plastic hinge forming. OK?
All right. We have a few more minutes.
AUDIENCE: That kind of looks like plastic buckling.
LORNA GIBSON: Well yeah, it's not buckling, but it's plastic, yeah. It's permanent. Anyone else? OK. No other questions? Should we call it a day? Is that helpful? All right, then. It's what I do. Come on. It's what I do. All right. So I'll see you Wednesday. And my plan is to grade the tests before spring break, so I shall have it back to you.
Free Downloads
Video
- iTunes U (MP4 - 151MB)
- Internet Archive (MP4 - 151MB)
Subtitle
- English - US (SRT)