Flash and JavaScript are required for this feature.
Download the video from iTunes U or the Internet Archive.
Description: Themal properties and behaviors of foams is covered in this session.
Instructor: Lorna Gibson
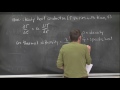
Lecture 9: Foams: Thermal P...
The following content is provided under a Creative Commons license. Your support will help MIT OpenCourseWare continue to offer high quality educational resources for free. To make a donation or view additional materials from hundreds of MIT courses, visit MIT OpenCourseWare at OCW.MIT.edu.
PROFESSOR: So what I wanted to do today was talk about thermal properties of foams. And foams are often used for thermal insulation. And that's always closed cell foams that are used for thermal insulation. And we'll see why. And the foams tend to have a low thermal conductivity. And that's largely because gases have lower conductivity than solids. And if you have mostly gas, you're going to have a lower conductivity. So they have a low conductivity because they have a high volume fraction of gas. And they've got a low volume fraction of the solid.
They also have cells. And the heat is transferred partly by radiation and convection. And if you have small cells, you reduce the amount of convection and radiation. And we'll see that. So that, by having a cellular structure, and in particular, by having small cells, you can decrease the heat transfer.
OK, so let me write some of the stuff down.
So closed cell foams are widely used for thermal insulation.
And the only materials with lower thermal conductivity than closed cell foams are aerogels gels.
And I'll I talk a little bit more about aerogels later on today. But the difficulty with aerogels is that they tend to be very weak and brittle, like ridiculously weak and brittle. So we had a project on aerogels a couple of years ago. And the students who I was collaborating with would make aerogels. And they'd bring it up to my office. And I would pick it up and like-- I would pick it up like this, and it would break. So they have very low thermal conductivity, but they're very brittle. And I brought a few of our samples of aerogels, just so you can see what they look like. And I'll pass them around in that little tube, so you can kind of play with them.
OK, so we're going to focus on foams. And whoops-- And we can say the low thermal conductivity of foam arises mostly from the high volume fraction of gas and that the gas has a low lambda, a low thermal conductivity.
So lambda is thermal conductivity, so I'm just going to put lambda there. Then it has a small volume fraction of solid, which has a higher thermal conductivity. And then the foams have a relatively small cell size. So one of the things we're going to look at is how does the cell size effect the thermal transfer, the thermal conductivity.
OK, so there's lots of applications for foams. And I guess one of the main ones is in buildings, insulating buildings-- also insulating refrigerated vehicles, things like LNG tankers. So there's lots of the applications for using foams for thermal insulation.
Foams, in addition to having a low thermal conductivity, they also have good thermal shock resistance. So thermal shock is if you have a material, you heat it up, and then you suddenly cool the surface of it, for example. So say you takes something and you quench it in water or quench it in some fluid, then the surface, it wants to shrink because its temperature drops, but it's connected to everything underneath it and it can't really shrink. And so it's constrained and you can get cracking and spalling. And so, it turns out foams have a good resistance to that thermal shock kind of loading. And we'll see why that is, too.
Roughly, you can see if the thermal expansion strain is the thermal expansion coefficient times the change in temperature. And the stress that you might generate is just going to be related to the modulus times alpha times delta-t. And because we're going to see that alpha for the foam is the same as alpha for the solid, but the E
foam is going to be a lot less that E of a solid would be. So because the modulus is smaller, you would get a better thermal shock resistance. OK, so I wanted to go over a couple of sort of laws of heat conduction, so we can talk about what thermal conductivity is and how we define it. So the first one here--
--first one here is for steady state conduction. So when we say steady state conduction, what we mean is that the temperature is constant with time, the temperature doesn't change with time.
So time's not going to come into the equation here. And heat transfer for steady state conduction, where there is no change in the temperature with time, described by Fourier's Law. And that says that the heat flux q is equal to minus lambda times the gradient in temperature. And if you want to think about just a one diversion of that, it's equal to minus lambda times dt by dx. So here, q is our heat flux. So that would have units of joules per meter squared per second. So how much heat transfer per unit area per unit time. Lambda is the thermal conductivity. And it has units of watts per meter k, so degrees kelvin. And then delta or-- and then this is our temperature gradient.
OK, so that's Fourier's Law, and we're going to use that later on when we talk about the foams. And then, just so that we have things a little more complete, if you have a non-steady heat conduction, if the temperature varies with time, then there's a difference equation that involves the thermal diffusivity. So if we have non-steady heat conduction-- so t varies with time. I'm going to call a time tau. Then a partial differentiation, the partial derivative of temperature with respect to time is equal to the diffusivity, that's given the symbol a, times the second derivative of temperature with respect of distance, so with respect x squared.
So here a is the thermal diffusivity. And it is equal to the thermal conductivity divided by the density and divided by the specific heat. So here, rho is the density and cp is the specific heat. The specific heat is the heat required to raise the temperature of a unit mass by the unit temperature. And so, the density times cp is the volumetric heat capacity. It's how much energy you would need to raise a certain volume by, say, 1 degree k instead of a certain mass.
OK, so on the table here, on the screen, we have different materials. And we have the thermal conductivity lambda. And we have the thermal diffusivity, a. And I guess I should also say a has units of meters squared per second. So this table is arranged in order of decreasing thermal conductivity. So here's copper at the top, 384, watts per meter k. Here's, you know, different metals. You've got aluminum. Here's a couple of ceramics. They're about a factor of 10 less than the metals. Here's the polymers, another factor of 10 less than that. And here's some gases. Air is about 0.025. Carbon dioxide is less than that. Triclorofluoromethane, which used to be used as a gas in foams because it's got such low thermal conductivity, is 0.008. But it's no longer used because it's a-- what you call it? A fluorocarbon. Anyway, it decreases our ozone layer. So they don't use that anymore.
Now here's some wood. So that's one sort of cellular solid. And they're around 0.04-- something like that. And here's a group of polymer foams. And they're a little over 0.025. So if you think of-- if you had the gas, air-- if the air was the gas inside the foam, 0.025 is lambda for the gas. So you're not going to get lower than that. And you have to use a low conductivity gas to get these values, like 0.025 here, 0.020, 0.017. And then, hear some other sorts of sort of mineral fibers, glass foams, glass wools. OK, so that's just a table so that you have some data there. All right? Yes?
STUDENT: [INAUDIBLE] --foams, if they are closed cell, with a different gas rate. Because if they're open cell--
PROFESSOR: --Right. The gas is going to--
STUDENT: --it would just always be air.
PROFESSOR: It's going to go. And in fact, one of the difficulties with using the lower conductivity of any gases is there's a phenomenon called aging, that if, you know, you've got your gas inside your foam, it's going to diffuse out into the air. And air's going to diffuse in. So over time, the thermal conductivity tends to increase because you're getting air coming and the local-- conductivity gas going out. But I think, typically, that process takes a number of years. It doesn't happen in a week. But if you're designing a building and want the building to be there for 50 years, it occurs faster than that. So it's not ideal from that point of view.
All right. So let me talk a little bit more about thermal diffusivity. Let me scoot over here.
So materials with a high value of that thermal diffusivity, a. They rapidly adjust their temperature to their surroundings. So if they have a high value of a, what it really means they've got a, say, a high value of lamda-- so high thermal conductivity. And, say, a low value of this volumetric heat capacity. So it doesn't take much energy to change their temperature. And they also conduct heat well. So they tend to adjust their temperature to their surroundings quickly.
OK, so then, let's talk about the thermal conductivity of a foam. So I'm going to call that lambda star. So the star is the foam. And then we'll talk about-- lambda s will be the lambda for the solid that it's made from. So if you think of the thermal conductivity of the foam, there's contributions from different types of heat transfer. So you could have conduction through the solid. I'm going to call that lambda s. You could have conduction through the gas. You could have convection within the cell. So convection has to do with having, say, within the cell, it might be a different temperature on one side of the cell to the other side of the cell. And the warmer side of the cell, the gas is going to tend to rise to the warmer side and fall to the cooler side. And you get a convection current set up. So you can get heat transfer from that. And you can also get heat transfer by radiation. So radiation can cause heat transfer, as well.
So we're going to have contributions from conduction through the solid. So the amount of conduction in the foam from the solid-- I'm going to call lambda star s. So lambda s would be the conductivity of the solid. And lambda star s is the thermal conductivity contribution from the solid in the foam.
So we get kind of-- through the solid. We have conductivity through the gas. So it's lambda star g for gas. And then we could have convection within the cells. We'll call that lambda star c. And then we could get radiation through the cell walls and across the voids. We'll call that lambda star r. And so, the thermal conductivity of the foam is just the sum of those four contributions.
So we're just going to go through each of those contributions, in turn, and work out how much thermal conductivity you get from each of them. And it turns out most of the thermal conductivity comes through the gas. So if we first look at just conduction through the solid, we've got that contribution to the conductivity of the foam from the solid, it's just equal to some efficiency factor times the thermal conductivity of the solid times the volume fraction of the solid or the relative density. And here, eta is an efficiency factor. And it accounts for that tortuosity in the foam. So if you think of the solid in the foam, it's not like we have little fibers that just go from one side to the other like this and the heat just moves along those fibers. You know, the foam cells have some complicated geometry and the heat has to kind of run along that complicated geometry.
And people have made estimates of what this is. And it's roughly a factor of 2/3. So I guess it would depend on exactly the foam cell geometry. But typically it's around 2/3. So that's conduction through a solid. That's straight forward. Conduction through gas is similarly straightforward. It's just the conductivity of the gas times the amount of the gas. And the volume fraction of the gas is just 1 minus the volume fraction of the solid. So it's just 1 minus the relative density. So the conduction through the gas is just lambda g times 1 minus the relative density.
So we can do a little example here. And you can see how much of the conduction comes from the solid in the gas. So for example, if we look at a foam that's 2.5% dense and say it's a closed cell poly-- what are we doing-- polystyrene. So the total thermal conductivity of the foam is about 0.04 watts per meter k. And the thermal conductivity of polystyrene is 0.15 watts per meter k. And the thermal conductivity of air is 0.025.
So let's assume it's just blown with air. And then if I just add up, what's the contribution of conduction through the solid and conduction through the gas-- so I just use those two little equations-- conduction through the solid-- it's going to be 2/3 of this value of lambda s times the amount of the solids-- that's 0.025 and then plus lambda g, which is 0.025 times the amount of the gas, which is 0.975. And if I work those two things out, this is 0.003 and this is 0.024. So that total is 0.027 watts per meter k.
So you can see if the total is 0.04, most of it's come from the gas. A little bit's come from the solid. And the rest is going to be from convection and radiation. And that's typical.
And that's the reason that they sometimes use low thermal conductivity gases to blow foams for thermal insulation because the gas makes up such a big fraction of the total conductivity. If you can reduce that, you reduce the overall conductivity.
So, we'll say foams for insulation are blown with low conductivity gases. But as I mentioned, you have this problem with aging that, over time, that gas is going to diffuse out and air is going to diffuse in.
Then the overall thermal conductivity of the foam is going to increase.
So that's the conduction. And then the next contribution is from convection. So imagine we have one of our little cells here. And it's hotter on that side than it is on that side. And hot air is going to rise. Cold air is going to fall. So you get a convection current set up. And because of the density changes, you get a buoyancy force in the air. So that's kind of driving the convection. But you also have a viscous drag. So the air is moving past the wall of the foam. And there's going to be some viscous drag associated. And how much convection you can get depends on the balance between this buoyancy force and the viscous drag.
So we'll say the gas rises and falls due to density changes with temperature. And the density changes give rise to buoyancy forces. But we also have these viscous forces from the drag of the air against the walls of the cell.
So air moving past the walls-- this is kind of a fluid mechanics thing-- so that air is a fluid. And in fluid mechanics, they often use dimensionless numbers. And there's a dimensionless number called the Rayleigh number. And the Rayleigh number, you can think of it-- it's not quite the balance of the buoyancy force against the viscous forces. But it involves those forces. And convection is important if this Raleigh number's over 1,000.
And here's what the Rayleigh number is. It's the density of the fluid times the acceleration of gravity times beta. Beta's the volume expansion coefficient for the gas-- times the temperature change. And we're going to look at a temperature change across a cell. And then, times the length. That's going to be the cell size. And we divide that by the fluid viscosity and the thermal diffusivity.
So let me write down what all these things are. So rho is the density of the gas. So the g's gravitational acceleration. Beta is the volume expansion of the gas. And for a constant pressure that's equal to 1 over the temperature. Then delta tc is the temperature difference across a cell. And l is the cell size. Mu is the dynamics viscosity the fluid. And a is our thermal diffusivity.
So what I'm going to do is just work out, for a typical example, how big of a cell size do you need to get this Rayleigh number to be 1,000. And we're going to see that, typically, that cell size is big. It's like 20 millimeters. So in most foams, the convection really isn't very important at all. So it's typically-- people don't worry about convection. And let me just show you how that works.
So for our Rayleigh number, which is ra-- for the Rayleigh number to be 1,000-- say we had air in the cells. And say the temperature was room temperature. Then the volume coefficient of expansion is just 1 over t. So it's 1 over 300, say. degrees k to the minus 1. Let's say our change in temperature across one cell was 1 degree k. Bless you. The viscosity of air is 2 times 10 to the minus 5, pascal seconds. The density of air is 1.2 kilograms per cubic meter. And the thermal diffusivity for air is 2 times 10 to the minus 5 meters squared per second. And if you plug all of these into that equation for the Rayleigh number and you solve for the cell size, you find that the cell size, l, is 20 millimeters. So that says convection is only important if the cell size is bigger than that.
And so most foams have cells much smaller than that. And convection is negligible.
So I have enclosed cells and the heat's not transferred so easily from one cell to another by the gas moving. And by having small cells the convection drops out. So you don't have to worry about that. So the last contribution to heat transfer is from radiation. And there's something called Stefan's law that describes the heat flux for radiated heat transfer from a surface at one temperature to another surface at a different temperature across a vacuum. So we can say we have a heat flux qr not from a surface of one temperature. So I'm going to call that t1-- to one at a lower temperature. I'm going to call tnot-- with a vacuum in between them.
So this is [? Stefan's ?] law so this is the radiative heat flux is equal to the emissivity of the surfaces, which is beta 1 times a constant called Stefan's constant-- sigma times the fourth power of temperatures. I'm taking the difference of the temperatures so here are the Stefan's Constant-- is sigma. And that's equal to 5.67 times the 10 to the minus 8. And that's in watts per meter squared per k to the fourth. And beta is a constant describing the emissivity of the surfaces.
So it gives the radiant heat flux per unit area of the sample relative to a black body. And that's a characteristic of the emissivity. All right, so then, so if we-- yes?
STUDENT: [INAUDIBLE]
PROFESSOR: Now-- so right now, forget the foam. We have no foam. We just have two surfaces with a vacuum between them. And now I'm going to stick a foam between the surfaces. And we're going to see how that changes the heat flux, OK? So the next step is we put the foam between those two surfaces. And the heat flux is going to be reduced because the radiation is going to be absorbed by the solid and reflected by the cell walls. And so we're going to characterize how much it's reduced. So there's another law called Beer's Law, which characterizes the reduction in the heat flux.
Piece of chalk's getting to small
OK, so Beer's Law gives us the attenuation, so the sort of reduction in the heat flow. So qr is equal to qr not. That would be the heat flux, if we just had the vacuum. And then there's an exponential law. And it's the exponential of minus k star t star. And here, k stars in an extinction coefficient for the foam. Talk a little bit more about that in a minute. and t star is just the thickness of the foam. And then this thing is called Beer's Law.
So we have very thin walls and struts. And we're just going to consider optically thin walls and struts to make life easy. Then we can say that, if they're optically thin, they're transparent to radiation. They're optically thin if they're less than about 10 microns. Then this extinction coefficient is just the amount of solid times the extension coefficient for the solids. So it's just the relative density times the extinction coefficient for the solid.
OK, and then I can say, the heat flux by radiation. I can use two equations to write that down now. And then I'm going to let them be equal to get the thermal conductivity. I can say qr is going equal to lambda r times dt by dx. So that's the Fourier's Law that we started out with. And then I've also got the qr that I'm going to get by combining the Stefan's Law with the Beer's Law up there. So if I do that, I get that qr is beta 1 times sigma times t1 to the fourth minus t not the fourth. So that's the qr not up there from down there. And then I've got an exponential for the attenuation. And instead of k star, I'm going to put the relative density of times ks. and then I've got the thickness of the foam, t star, as well.
OK, so that's qr, but that has to equal lambda times dt by dx. So I'm going to use some approximations. Here and I'm going to end up with an expression for the contribution from radiation to heat transfer in the foam. Yeah?
STUDENT: So when you say optically thin walls, where t is less than 10 microns, you mean like the walls of the foam?
PROFESSOR: Yeah, yea.
STUDENT: So it's different t than the--
PROFESSOR: t star is the thickness of the whole thing, yeah. So imagine we had our two surfaces. And they might be like 100 millimeters apart or something. t star is the sort of thickness of the foam in between the two surfaces. And the optically thin is the cell walls, which are microns kind of thickness. OK.
So I'm going to make some approximations here. And that's going to allow me to solve for t star. So I'm going to say that dt by dx x is approximately equal to just t1 minus t not over the thickness of the foam or I'll call that delta t over t star. And then, the other approximation I'm going to use is that t1 to the 4th minus t not to the fourth is equal to 4 times delta t times the average temperature cubed. So here t bar is the average temperature, t1 plus t not over 2.
So then, if I use those two approximations, I can write that qr, our heat flux from radiative transfer. I got the beta 1. I've got the sigma. And instead of the difference of the fourth power, I'm going to write 4 delta t t bar cubed. And then I've got my exponential. Blah, blah, blah, blah, blah. So then, here's the relative density times ks times t star, the overall thickness. That's going to equal the radiative contribution to the thermal conductivity of the foam. And instead of dt by dx, I'm going to have delta t over t star here. So part of the reason for doing these approximations I end up with a delta t term on both sides. Now I can cancel that out. And if I just take this mess here and multiply it by t star, then I've got lambda r star.
That's our thermal conductivity contribution from radiation. So one of the things to notice here is that, as the relative density goes down, then the contribution from radiation to the thermal conductivity of the foam goes up.
OK, so this chart here shows thermal conductivity as a function of relative density. And it breaks down the contributions from the gas, g, the solid, s, and the radiation, r. And you kind of see the gas contribution doesn't change that much. These are relative densities between a little over 2 and a little less than 5%. So the amount of gas-- it's mostly gas in all of these things. The solid contribution increases as the relative density increases. So you'd expect that. And then, as I just said, as the relative density goes down, the amount of radiation contribution goes up. And so you can kind of see how that all fits together.
Another plot that shows the thermal conductivity versus the relative density. These are for a few different types of foams. You can see for this plot here, you reach a minimum in the thermal conductivity. And that's because you've got this trade off between the contribution from the solid and the contribution from the radiation. And those two kind of trade off and you get to a minimum. So let me write some of this down.
So I'll just say that-- hang on. Write this over again. This is looking at the overall thermal conductivity. And we can see the relative contributions of lambda, solid, lambda, gas, lambda, radiation. I'll just say this shown in the figure. I'm going to say the next figure shows a minimum in the thermal conductivity. Then I'll just say there's a trade off between the conduction through the solid and I can direction from the radiation.
And then we also have a plot here that shows the conductivity versus the cell size. And you can see that the conductivity increases with cell size. And the reason for that is the bigger the cells get, the radiation is reflected less often.
And one thing I wanted to mention with the cell size is that if you look at aerogels, the way aerogels shells work is that they have a very small cell size, a very small pore size. So typically, it's less than 100 nanometers. And the mean free path of air is 68 nanometers. So the mean free path is the average distance the molecules move before they collide with another molecule. And if your pore size is less than the mean free path, then that reduces the thermal conductivity. It reduces the ability of the atoms to pass the heat along between one another. So the way the aerogels work is they have a very small pore size. And what's important is how big the pores are relative to the mean free path of air.
OK, so that's the thermal conductivity. I wanted to talk about a few other thermal properties of foams, as well, today.
So one is the specific heat. And since the specific heat is the energy required to raise the temperature by a unit mass, then the mass is the same-- you know, if you have a certain mass of foam or a certain mass of solid-- the specific heat from the foam is the same as the solid.
So the specific heat for the foam is the same as the specific heat for the solid. So that would have units of joules per kilogram per degree k. And the next property is the thermal expansion coefficient. And it's a similar thing. The thermal expansion coefficient for the foam is equal to the thermal coefficient of expansion for the solid. So imagine you have-- say you had something like a honeycomb. If you heat it up a certain amount, every member is going to expand by alpha. And if every member expands by alpha, the whole thing expands by alpha. And this is the same. And it's the same idea with the foam. So if every member just gets longer by alpha, then the whole thing gets bigger by alpha.
OK, so the last topic I wanted to talk about was the thermal shock resistance. And thermal shock is the idea is that if you have something that's hot, and say you quench it in a liquid-- so you put it suddenly in a liquid-- the surface is going to cool down faster than the bulk of it. And because the surface is trying to contract because it's cooling down, but it's attached to the bulk of it and it's constrained, it can't really cool down, then you generate stresses. And if the stresses are big enough, you can cause fracture and have the thing crack and spall.
So we'll say if the materials is subjected to a sudden change in the surface temperature, that induces thermal stresses at the surface and can induce spalling and cracking.
So we're going to think about a material at one temperature that's dropped into, say, a liquid at a different temperature.
So the surface temperature is going to drop to the cooler liquid temperature and it's going to contract the surface layers.
And the fact that they're bound to the layers underneath that are not contracting as quickly, it means that you generate a thermal strain.
So the thermal strain is going to be the coefficient of thermal expansion times the change in temperature.
So you're going to constrain the surface to the original dimensions. And then you're going to induce the stress.
So if it's a plane or thing, it's e alpha delta t. And then, there's a factor of 1 minus nu, just because it's a plane, in a plane. And then you'll get cracking or spalling when that stress equals some failure, stress. So I can rearrange this and solve for the critical delta t that you can withstand without getting cracking. So I just rearranged this and say sigma's equal to sigma f. That would be sigma f times 1 minus nu over e and over alpha. So that's the critical change in temperature to just cause cracking.
So now what I can do is I can substitute in there for what you would have for the foam. And I'm going to do it just for the open cells just because it's easier to write the equations. So for the foam, I would have some sort of fracture strength. So when we did the modeling of the foams, we said that was equal to about 0.2 times the modulus of rupture times the relative density to the 3/2's power and 1 minus nu. And if I divide by the modulus of the foam, that's es times the relative density squared. And then we just had alpha for the foam was the same as alpha s. So then, I can rearrange this slightly and say it's equal to 0.2 over the relative density to the 1/2 power. So I'm canceling out these relative densities here.
And then I can combine all the solid properties together. And I'm going to say that nu for the solid is about equal to the same as nu for the foam.
So what I can do here is I can group all the solid properties together. And this just is delta t critical for the solid, right? So this is saying that the critical temperature range before you get cracking in the foam is equal to the range for the solid, but multiplied by this factor of 0.2 and divided by the square root of the relative density. So if the square of-- the relative density is going to less than 1. So this number here is going to be bigger than 1. So it's saying that the temperature range that will give you spalling in the foam is going to be bigger than the temperature range in the solid. So the foam's going to be better than the solid, OK? And that uses our little models from before.
So I think I'm going to stop there, probably cause my throat is starting to get too sore. There's a little case study in the notes. And I'll just put that on the notes on the Stellar site. It's like one page and it's really straightforward. You can just read that, OK? So this is the end of the bit on thermal conductivity. That's just this one lecture. And this is really the end of the whole section on modeling of the honey combs and the foams. So that's kind of the first half of the term is modeling the honey combs and the foams. And the second half of the term, we're kind of applying those models to different situations.
So next week, we'll have the review on Monday, have a test on Wednesday, week after that is Spring break. I can't believe we're at Spring break already. And then after that we'll start we'll do the trabecular bone for a week. We'll do tissue engineering scaffolds and cell mechanics for two or three lectures. We'll look at some other applications to engineering design, look at energy absorption and sandwich panels. And then, I'm going to talk about plants a little bit at the very end, OK? So we've already covered a lot of the kind of deriving equations part of the course. The rest of the course is more applying the equations to lots of different situations, OK? So I'm going to stop there just because my throat is giving out.
Free Downloads
Video
- iTunes U (MP4 - 131MB)
- Internet Archive (MP4 - 131MB)
Subtitle
- English - US (SRT)