Flash and JavaScript are required for this feature.
Download the video from iTunes U or the Internet Archive.
Description: Modeling mechanical behavior of honeycombs and out-of-plane properties are discussed.
Instructor: Lorna Gibson
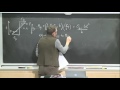
Lecture 5: Honeycombs: Out-...
The following content is provided under a Creative Commons license. Your support will help MIT OpenCourseWare continue to offer high quality educational resources for free. To make a donation or view additional materials from hundreds of MIT courses, visit MIT OpenCourseWare at ocw.mit.edu.
LORNA GIBSON: All right. I should probably start. Last time, we were talking about the honeycombs and doing some modeling of the mechanical behavior and we started off talking about the in plane behavior.
We're talking about loading it in this direction or that direction there. And we talked about the elastic modulus. I think I derived a Young's modulus for the one direction, a Poisson's ratio for loading in the one direction.
And then we started talking about the stress plateau and we went over the elastic buckling stress, for one of these elastomeric honeycombs like this. And we went through the plastic collapse stress, for, say, a metal honeycomb that would yield. And I think I started talking about a brittle honeycomb and brittle crushing.
The idea with a brittle honeycomb-- like a ceramic honeycomb-- is it could fail in a brittle manner. And the failure is going to be controlled by the cell wall in bending. And when that bending stress reaches the modulus of rupture, or the bending strength of the material, then you get wall fracture. I think that's where we left it last time, right? I had written down something about cell wall fracture.
Now, I wanted to do the little derivation. Here's our little schematic up here. Here's the honeycomb. You've loaded it with sigma 1 here to such an extent that one of these cell walls has reached the modulus of rupture and has broken. And this is the little free body diagram that corresponds.
I'm going to go through sigma 1 for loading in the one direction. This is the same thing for loading in the two direction. And the result for that's in the book.
OK. If I have loading in the one direction, I can relate that horizontal force p to the stress in the one direction. The little p is equal to sigma 1 times h plus sin theta times b. And remember, b's the depth into the page. And I'm going to define sigma fs as the modulus of rupture of the cell wall material. It's the bending strength of the cell wall material.
And we're going to say that we get fracture of that bent wall when the applied moment is equal to the fracture moment. From the plastic collapse stress from last time, we had the applied moment was equal to p times l sin theta over 2. That was just using static equilibrium, looking at that free body diagram of the beam.
And if I write p, in terms of sigma 1 up here, I can just write that like this sigma 1 times h plus l sin theta times b. And then I've got this other term of l sin theta and we divide that whole thing by 2.
That's the applied moment. And we're going to get fracture when we reach the fracture moment. I'm going to call that mf-- the moment at fracture.
Last time, we figured out a plastic moment to form a plastic hinge. And this is an analogous thing. But in this case, remember, if we have a beam and we have the stress profile through the cross section of the beam, it's going to look something like that.
So for our beam, that's going to be the thickness of the beam there. So if it's linear elastic, we get the maximum stress at the top and the bottom. And the neutral axis is here in the middle. There's no stress there.
This is the normal stress distribution here. And as we increase the stress for a brittle material that's going to be linear elastic till fracture, this is going to stay linear like this until we reach this modulus of rupture stress here. When we reach that stress, then we're going to get fracture of the beam.
And we can say that there's some moment associated with that. I could say that this stress block here is equivalent to some concentrated force and this stress block down here is also equivalent to the-- it's going to the same magnitude, but the opposite direction force. And I can get the fracture moment by figuring out how big those forces are and multiplying by this moment arm between the two forces. OK?
The magnitude of those forces is just going to be the volume, essentially, of this stress block here. Imagine there's stresses there. It's a triangle, so the area of it's going to be a half times t over 2 times of sigma fs. And it's going to go b into the page.
So if you think of the force-- if this was the stress-- if that stress was constant, it would just be sigma fs times b times t. But it's not constant. It's a linear relationship. So I'm taking the area of that triangle.
That's the force. And then I want to multiply that times the moment arm. And the moment arm between those two forces-- each of these forces acts through the centroid of the area. The centroid of the area is not in the middle for a triangle, and that total distance is 2/3 of the thickness, t. OK? That's the moment arm that you get by figuring out where the centroid of these areas are.
I multiply that times 2/3 t and one of the 2's is going to cancel. I can rewrite that and sigma fs times b times t squared over 6. OK?
I think, last time when we talked about the plastic moment, we did a similar calculation and it worked out to sigma y bt squared over 4. So now this is sigma fs, the modulus of rupture, times bt squred over 6. The 6 is just slightly different because we've got a triangle here instead of a square shape like we had before.
And now I can get the brittle crushing strength and compression by just equating that applied moment to this fracture moment. And if you do that, the result you get is this plateau stress for brittle crushing and compression.
In the one direction, it's sigma fs-- the modulus of rupture of the cell wall-- times t over l squared. And then divided by a geometrical factor. And her regular hexagons, it works out to 4/9 of the modulus of rupture times t over l squared. OK? Are we good?
We've got the in plane compressive properties now. We've got the elastic moduli and we've got the three plateau stresses that correspond to the three mechanisms-- to the elastic buckling failure mechanism, the plastic yielding mechanism, and then the fracture mechanism for brittle crushing. OK?
If you think of the stress-strain curve of these materials in compression, the stress strain curves all look something like that. And now we've figured out equations that give us the modulus here and our collapse stress there. OK? So we can describe that stress-strain curve.
All right. That's compression. And the next thing I wanted to talk about is tension. And if we think about the tensile behavior, the elastic moduli are going to be just the same. So the moduli are the same in tension and compression.
And then, if we think about the stress plateau, we don't really have a stress plateau for an elastomeric material because there's no elastic buckling. If you pull it in tension, you're not going to get buckling in tension. You only get buckling if it's in compression.
If you have a material that yields like a metal, you can get a plastic collapse stress and a plastic plateau. And that's very similar in tension and compression. There's a very small geometrical difference, but you can, essentially, ignore it.
If you're loading the material in compression-- and imagine this was a metal-- if you load it in compression, the cell walls are getting a little further apart when I compress it. And if you're loading in tension, like this, the cell walls are getting a little closer together. So there's a small geometrical difference. But if we ignore that, we can say that the plateau stress for plastic behavior is about the same in tension and compression.
And so really, the only property that's left is to look at a brittle honeycomb. And for a brittle honeycomb, you can have fast fracture and we can calculate a fracture toughness. So this next slide describes the fracture toughness calculation that we're going to do.
Here's our honeycomb. I'm going to load it in the sigma 1 direction here. I've turned the honeycomb 90 degrees, so this is still sigma 1.
And imagine now that we've got a crack here. And I'm going to consider a situation where the crack is very large, relative to the cell size. So it's not a crack in the cell walls. It's a crack that goes through multiple cells.
I'm going to assume the crack is large, relative to the cell size. I'm going to assume that the bending is the main deformation mode. And what I'm going to do is look at-- if I have my crack tip here, I'm going to look at this cell wall a just ahead of the crack tip. And I'm going to say, that cell wall is bent. And I'm going to figure out something about the stress in that cell wall and look at when that fails.
And I'm going to assume that the cell wall has a constant modulus of rupture. So the cell wall has a constant strength. You can imagine the cell wall could have little tiny cracks in it, too. And if a cell wall has a bigger crack, it's going to fail at a lower stress. But let's imagine that the cell walls are all the same strength and they all have a constant modulus of rupture.
Let me write some of this down. In tension, the elastic moduli are going to the same as in compression. There's no elastic buckling in tension, so that's not going to happen. The plastic plateau stress in tension is going to be very similar to that in compression.
As I mentioned, there's a small geometrical difference, but we're going to ignore that. And then, if we had a brittle honeycomb, like one of those ceramic honeycombs I showed you, then we can have fast fracture. What we want to calculate is the fracture toughness. And I'm going to make a few assumptions here.
I'm going to assume that the crack length is large compared to the cell size. And if I do that, I can say that I'm going to use the continuum assumption. Hello. We'll come back to that.
I'm going to say that axial forces can be neglected. We're just going to look at bending forces. And I'm also going to assume that the modulus of rupture is constant for the cell wall.
First, let's just think again about the continuum. Imagine we just had a solid and we have a plate of the solid and it's loaded in tension with some remote stress-- some far away stress-- sigma 1. And the plate has a crack of length 2c perpendicular to that normal stress. And we're going to look at the stress-- local stress at the crack tip-- some distance r ahead of the crack tip there.
In fracture mechanics, it's been worked out what that local stress field is. And it depends on the crack length, and then how far ahead of the crack tip you are. So you can say that if you've got a crack length of 2c in a linear elastic solid, and the crack is normal to a remote tensile stress-- which I'm going to call sigma 1-- then that crack is going to create a local stress field at the crack tip.
And we're going to use this equation for the local stress field. The local stress field is equal to the far away field divided by-- or multiplied by the square root of pi c and divided by the square root of 2 pi r. So there's a stress singularity at the crack tip. And then the local stress decays as you move away from the crack tip.
AUDIENCE: And what is r?
LORNA GIBSON: r is the distance from the crack tip. So if that's the tip of my crack there, then r is my distance out.
OK. In the honeycomb wall, if we look at the crack here, and then we look at that cell wall a that's just ahead of the crack tip, that cell wall is bent. So in the honeycomb, we're going to be looking at the bent cell wall. And that wall is going to fail when the applied moment equals the fracture moment.
If we look at wall a, we could say that the applied moment is going to be proportional to p times l. Getting ahead of myself there. I'm going to do this-- because it's hard to say exactly where the crack tip is because there's a void there.
I'm going to use that argument here where I make everything proportional. The moment's going to be proportional to p times l on wall a. And the fracture stress is going to be proportional to sigma fs times bt squared.
Last time, we said it was sigma fs bt squared over 6. It's the same thing. I'm just dropping the 6 out.
And then I can also say that this applied moment, if it goes as pl-- p is just going to be my local stress times lb. And then I multiply times l. So if you think of just thinking about-- if you got a load p on this member here, l, there's going to be some local stress there. And p is just going to be that local stress times the cell wall length times the width into the page.
And then, that local stress, sigma l, I can replace with that equation over there. So that local stress is going to go as sigma 1 times the root of c over the root of r. And I'm going to say the distance ahead of the crack tip goes as l.
Instead of having r, I'm going to say it's l. It's not necessarily exactly l, but it's going to be some fraction of l. That's my local stress there.
And then I've got an l squared times b. And if I set that equal to the fracture moment, that's going to be proportional to sigma fs bt squared. Are we good here?
You have to think of the crack tip. And there's some local stress field ahead of the crack tip. And we're saying that the load p is equal to that local stress times a cell length times the depth into the board. And then multiply it times l to get the moment. And then I replace that local stress with this standard equation for the remote stress and the crack length and the distance ahead of the crank tip.
So here, the b's are going to cancel out. And now I can solve for a fracture stress in the one direction. And that's going to-- well, let me get proportional-- that's going to be proportional to sigma fs. Then there's going to be a t over l squared. And then, this is going to go as the square root of l over c like that.
And now, if I want to get a fracture toughness, the fracture toughness is just the strength times the square root of pi times the half crack length c. So here, my fracture toughness is just that strength times the root of pi c. So I can say that's equal to a constant times sigma fs times t over l squared. And now, times the square root of l. These root of c's have canceled out.
So that's my equation for the fracture toughness. And one of the interesting things here is that the fracture toughness depends on the cell size. This is the first property that we've derived an equation for where it depends on the cell size.
OK. And here, c's just going to be a constant. All right. Now we've got a set of equations that describe the in plane properties.
We've got equations that describe the linear elastic moduli in the plane. We've got three equations that describe the compressive stress for elastic buckling failure, for plastic yielding failure, and for a brittle crushing failure. And we've got an equation for the fracture toughness, as well. OK? We've got a description of the in plane behavior of these hexagonal honeycombs.
The next thing I wanted to do was talk a little bit about in plane behavior, but for a different cell shape-- for triangular honeycombs. Because they deform by a different mechanism. And they can be used to represent the lattice materials that we looked at earlier, too.
If we have a triangular honeycomb with triangular cells, triangulated cells behave like a truss. And you can analyze trusses by just saying that the joints are pin jointed. There's no moments at the end of the joints or end of the members.
And the forces are all axial and so the behavior's a little bit different. I wanted to show you how these triangular honeycombs work, too. I can scoot this up.
Imagine that you've got a honeycomb that's an array of triangular cells like this. And say we're applying some bulk stress sigma to it, like that. And say it's got a depth b into the page.
When we have a triangulated structure like this, it behaves like a truss. And we can analyze it as being a pin-jointed structure. There's no moments at the joint.
And if it's pin-jointed and there's no moments at the nodes, then we just get axial forces along the members. And even if the nodes were fixed-- as they are in these ceramic honeycombs-- you can show that if it's triangulated, even if you accounted for any bending, it really is a very tiny contribution to the deformation in the forces. It's less than a couple of percent. I'll say even if the ends are fixed-- I'll just say the bending contributes less than 2% to the forces in the deformation. If I have a triangular cell like that, and say I pick a unit cell like this, and I say that the bulk stress produces a load of p on the top and p over 2 at each of the bottom nodes there, then the force in each member is going to be proportional to p.
And for a given geometry of triangle, you can figure out exactly what the force distribution would be in each of the members. But I'm going to use one of these proportional arguments again, just to get a general result. Because I don't really care that much about the details of the geometry.
OK. If I have a little set up like this, I can say that the overall stress is going to be proportional to p over lb. And the stress in each member is going to be proportional to p over l times the thickness-- or b times the thickness.
This is the overall stress. The overall strain is going to be proportional to some deflection of the triangle divided by the length. So if I said, say, this length here was a length l. And then the deflection of each member is going to be proportional to p times l over es times the cross sectional area of the member, and that's just b times t. OK? So this is the stress on the whole thing, the strain on the whole thing, and relating the delta to the p.
And then, the modulus of the whole honeycomb is going to go as the stress over the strain. So that's p over lb divided by delta over l. These l's here cancel.
And delta here is pl over es bt, and so the b's cancel and the p's cancel. And the modulus I get for the honeycomb is just some constant related to the cell geometry times the modulus of the solid times t over l. And if you did an exact calculation for equilateral triangles, you'd find that that constant's 1.15.
The interesting thing to note here is that the modulus for these triangular honeycombs goes as t over l, not as t over l cubed. For the hexagonal honeycomb, it went as t over l cubed. And here, because the deformations are axial-- not bending-- it's much stiffer. And it's much stiffer to have one of these triangulated structures. I'll just say, here, that the modulus goes as t over l cubed for the hexagonal honeycombs due to the bending.
One of the reasons that people are interested in those lattice materials is that they, too, have moduli that go as t over l. That basically go with the relative density, rather than with the relative density cubed. So they're much stiffer than, say, a hexagonal honeycomb. OK? Are we good with the triangulated honeycombs? Yes?
AUDIENCE: What is c?
LORNA GIBSON: c's just a constant related to the cell geometry. For equilateral triangles, it's 1.15. You could work it out, but it just makes the whole thing a little more complicated to do that.
OK. That's the in-plane behavior. And next, I wanted to talk about the out-of-plane behavior. Remember, we said the hexagonal honeycombs are orthotropic and the orthotropic materials have nine elastic constants. And we've figured out four so far.
We've figured out the four in-plane elastic constants. There's five out-of-plane elastic constants to describe the elastic behavior completely. And so we want to talk about these other elastic constants.
The honeycombs are also-- I should just back up a little bit. The honeycombs are used in sandwich panels. And when they're used in sandwich panels-- I brought a little panel in with carbon fiber faces and a nomex core.
If you bend that panel like that, you're going to get shear stresses in the core. And the shear stresses are going to be going this way and this way on, and that way, that way on. And so those shear stresses are out-of-plane. They're in the x1, x3, or x2, x3 planes. And so you need the out-of-plane properties for the shear properties in the sandwich panels.
Honeycombs are also sometimes used as energy absorption devices. Not these rubber ones, but imagine there was a metal one. And when they're used for energy absorption devices, they're typically loaded this way on. Again, that's the out-of-plane direction and you need the out-of-plane properties.
And for the out-of-plane properties, the cell walls don't tend to bend. Instead, they just extend or contract. And you get stiffer and stronger properties. Let me just write something down and then we'll start to derive some of those properties. The cell walls contract or expand instead of bending, and that gives stiffer and stronger properties. OK.
OK. There's five elastic constants in the out-of-plane directions. We'll start with the Young's modulus. And if I take my honeycomb and I load it in the x3 direction-- just taking this thing here and just loading it like that-- the cell walls just axially contract and the stiffness just depends on how much cell wall I've got.
So the modulus in the three direction is just equal to the area fraction times the modulus of the solid. That's just the same as the volume fraction, or the relative density. So it's quite straightforward.
The cell walls contract or extend axially. e3 is just es times the relative density. And that's just es times t over l. And then there's a geometrical factor here. h over l plus 2 over 2. h over la plus sin theta times cos theta.
Again, a little bit like those triangular honeycombs. The thing to notice here is that in the three direction, the modulus goes linearly with t over l, whereas in the in-plane directions, it goes with t over l cubed. So there's a huge anisotropy in the honeycombs because of this difference.
Imagine a honeycomb might be 10% dense. t over l might be something like a tenth-- 0.1. So e star 3 is going to 0.1 of es, roughly, and in the other direction, it's going to be 1/1000th. So there's a huge anisotropy because of this.
Let me just-- square honeycombs. This just shows looking at the out-of-plane directions and the different stresses and properties that we're going to look at here. The next one we're going to look at is Poisson's ratio.
And first, we're going to look at loading in the x3 direction. And if we load it in the x3 direction, the cell wall's just strain by whatever the Poisson's ratio is for the solid times the strain in the three direction in the other two directions. We'll say for loading in the x3 direction, the cell wall's strain by nu of the solid times whatever the strain is in the three direction in the other two directions.
If we load it in the x3 directions and everything contracts by that much in the other two directions, that just means that the Poisson's ratios-- nu 3 1 and nu 3 2 are going to be the same. And they're just going to be equal to the Poisson's ratio of the solid. So if each wall is going to contract by that amount, the whole thing's going to contract by that amount. And that's going to give you that Poisson's ratio.
Let me just say, here, also-- and remember that I'm defining nu ij as minus epsilon j over epsilon i. We're loading in the three direction here.
And then you can get the other two Poisson's ratios using those reciprocal relationships. So nu 1 3 and nu 2 3 can be found from the reciprocal relations. And remember, those relationships come from saying that the compliance tensor, or the stiffness tensor, is symmetric.
We can write, for instance, that nu 1 3 over e1 is equal to nu 3 1 over e3. So I can write that like that. And then I can say nu 1 3-- that is going to equal to nu 3 1 times e1 over e3. And we just saw that nu 3 1 was equal to nu s.
And we see, from before, the e1 is equal to some constant. Let me just call it c1 times es times t over l cubed. And e3 is going to be some other constant times es time t over l. The es's are going to go.
And if t over l is small-- even if it's say, a 10th-- and this is going as t over l cubed and that's going as t over l, then I can say this thing is about equal to 0. It's going to be small. It's not to be exactly [INAUDIBLE] 0, but it's going to be small so we're going to say it's 0. So I'll just say for small t over l.
And then, similarly, nu 2 3 is going to be close to 0, as well. So there's the Poisson's ratios. We've got the Young's modulus, the Poisson's ratios, and next we want to get the Shear moduli.
And the shear moduli is little more complicated. The cell walls are loaded in shear but the neighboring cell walls constrain them and they produce some non-uniform strain. I'm talking about shearing it this way on.
You can see on this figure here, we're talking about shearing it, like tau 2 3 or tau 1 3, this way. And so each wall is going to shear, but the walls are attached to each other so they can't just do it independently. They have to be constrained by each other.
And the exact solution is a little bit complicated. And I'm just going to give you an estimate of what that modulus is. And we're going to see that it depends linearly on t over l, as well.
I'll just say the cell walls are loaded in shear. An estimate is g star 1 3 is equal to g of the solid times t over l times a geometric function. It's cos theta over h over l plus sin theta. And for regular hexagonal honeycombs, it's 1 over root 3 times gs times t over l.
Again, just note the linear dependence of the modulus on t over l. And in the book, there's a method using upper and lower bounds that gives an estimate for g 2 3. I'm not going to go into it.
I just want you to notice that the shear moduli go as t over l, just like the Young's modulus does. And Sardar, who's sitting in the back there, has done even more involved calculations and analysis of the shear moduli of the honeycombs in this direction. So I'm not going to go into all the gory details on that.
OK. That gives us the moduli now. So now we've got all nine elastic moduli. OK? And the next thing to do is, then, to figure out the compressive strength. So we're going to look at compression again, and then we'll look at tension.
If we look at compressive strengths, again, we've got different modes of failure. And if I have an elastomeric honeycomb like this one here-- if these cell walls were a little longer, I might be able to actually do it. If you compress this enough, you produce buckling in the cell walls. And this is a schematic of this buckling pattern here. And you can see there's a diamond pattern where it alternates up and down in the different cell walls.
We're going to do some approximate calculations, but you can see the idea of how the material behaves in this direction, just from these approximate calculations. OK. Say we have our honeycomb like this, and here's the prism axis this way. And now, we're going to load it up with some stress in the three direction. I'm going to call this sigma star elastic 3 when it buckles.
And what we're going to do is just look at a single plate. And look at the buckling of a plate. We're going to analyze it just looking at a single plate and then adding up how many plates we have per unit cell. It's actually more complicated than this because, obviously, the plates are attached together and there's some constraint by attaching the plates. But we're not going to worry about that.
If you have a column-- just a, say, circular cross-section column-- and you apply a compressive load to it, it buckles at the Euler load. And similarly, there's an Euler load for plates. And that equation is usually written as a p critical is equal to some end constraint factor. For plates, it's usually called k instead of n.
So this is an end constraint factor. It depends on the modulus of the plate. It goes as t cubed.
Then, there's a factor of 1 minus mu of the solid squared and the length of the plate. Say this plate here-- actually the width of the plate there is h and the length here is b. And this thickness here is t like that.
Here, k is an end constraint factor. And it's going to depend on the stiffness of the adjacent cell walls.
If I had a honeycomb, and say it was-- these walls here-- the adjacent walls-- were thicker, then you can imagine those thicker walls-- it'd be harder to get them to deform. And the end constraint for the plate is going to depend on those thicker walls. So that the end constraint, k, depends on these-- say I'm looking at this wall here of width h here, then how stiff these other two walls are is going to affect that end constraint factor.
What we're going to do is just do something very approximate. We're going to say if these vertical edges here-- if this edge here and that one there-- if they were simply supported-- if they're just pinned to the next column, the next member-- then k has some value. And if they're fixed, it has some other value. And we're going to pick a value in between. So we're going to do something very approximate.
I'll say if those vertical edges are simply supported-- that means they're free to rotate-- then k is equal to 2.0. And this is if b is bigger than three times the length. So this is h here, or we could say l. Either way. It's really the-- it's the length when we look at the honeycomb this way on, but it's the width in that picture there.
And if the vertical edges are clamped, or fixed, then k is equal to 6.2. These are values you can look up in tables of plate buckling. And we're just going to approximate it by saying k is equal to 4. We're just picking a value that's in between those two.
And then, the p total is going to be the sum of the p criticals for the columns that make up a unit cell. For the unit cell, I have one wall of length h and two of length l. And if you just take that total load and divide by the area of the cell, you get that this compressive strength for elastic buckling is approximately equal to es over 1 minus nu s squared times t over l cubed. And then there's a geometrical factor here. And if you had regular hexagonal cells, this buckling stress works out to 5.2 times es times t over l cubed.
If you remember, for the loading in the two direction-- in the in-plane direction-- it has the same form. And goes as es times t over l cubed, but it's much smaller. This number here was, I think, 0.2. It was much smaller. So it has the same form, but it's a lot bigger.
OK? Are we good with that? The idea is we just use the standard equations for plate buckling. We make some estimate of what that end constraint factor is. And we just have an approximate calculation here.
OK. That's the elastic buckling. If I had a metal honeycomb, then it might not fail by elastic buckling like that. Instead, we'd probably get yielding.
If it was dense enough, we could just get axial yielding that-- if you just loaded it, you'd have axial forces. And at some point, you'd reach the yield stress. And so you can get failure by just uniaxial yield. That's one option.
And if you get that, then it just depends on how much solid you've got again. So it's just the yield strength of the solid times the relative density. But usually, the honeycomb is thinner walled than that. And usually, you get plastic buckling proceeding that.
In plastic buckling, you can think of it as-- say if you have a tube-- this is just shown for an individual tube here. You can see how the tube folds up. And you can get that same kind of thing with the honeycomb.
Here's a single tube. It's been loaded along the prism axis of the tube. And you can see, you get these folds, and the more you load it, the more number of folds you get. And the more the folds concertina up.
To do an exact analysis for the honeycombs, you would have to take into account not just one tube, but the constraint of the neighboring tubes again. And again, that gets to be a complicated, messy thing. So again, we're going to do a more approximate thing.
What we're going to do is just say that we have members that are folding up like that. So the same geometry. But we're just going to look at a single cell wall and see what the single cell wall does. And someone else has done the more exact calculation. We'll just compare our approximate calculation to the exact one.
OK. We're going to consider an approximate calculation. What we're going do is look at our isolated cell wall. And if you look at the figure here, the wall is going to be vertical, initially.
And as we load it, eventually it's going to buckle and we're going to form one of those plastic hinges in the middle here. And then, the thing is then going to rotate about that plastic hinge and just fold up. So at the bottom here, it's completely folded up. OK?
And we're going to do a little work calculations. We're going to look at the internal work done and we're going to look at the external work done. The external work is just going to be this load p times that deflection delta that the p moves through.
And if we say this is half of a wavelength-- if you think of this thing going through multiple wavelengths, just consider when it folds up like that, that's a half of a wavelength. It would go two of those to get a full wavelength. That's lambda over 2.
And so to go from this stage to that stage over here, the external work done is going to be approximately p times lambda over 2. Say that it's thin and that 2t is small compared to lambda. So it's going to be about p times lambda over 2.
And then, we're also going to look at the work done by the plastic moment. And when we form the plastic hinge here, there's a plastic moment. And that moment is going to rotate through an angle of pi.
So we start out straight here, we end up folded up like that, and we've gone from straight to that. We had to go through 180 degrees to get there. So it goes through an angle of pi. And if you have a moment going through a rotation, the work done is the moment times the rotation.
We're going to equate those two works done. We're going to look at the rotation of the cell wall by an angle of pi at the plastic hinge. Our plastic moment-- it's going to be the yield strength of the solid again times t squared over 4, the same as when we were talking about the plastic moment before for the other loading direction.
But now, instead of multiplying this times b, we're multiplying it times 2l plus h. That's the length of the cell wall that's associated with one cell. And now, it's not b because now we've turned the thing the other way on. We're loading it the other way on.
And this plastic hinge-- if I think of-- if this was b before. And now that b is l plus 2h-- or 2l plus h, rather. That's the dimension of the-- let me draw a little hexagon so maybe you can see.
OK. Now we're forming a plastic hinge halfway down the board. Imagine that this has some length b that way and we're halfway down the board. And now, the plastic hinge has to form all the way around these members here for one cell.
Or you could think about it as this guy plus these guys is one cell. You can think about the unit cell different ways, but it's one h plus two l's. OK? Are we OK with that?
OK. Then the internal plastic work is that plastic moment times the rotation pho-- or pi, rather. Sorry. Are we OK with this? That the work done is m times our angle?
Imagine-- let me get rid of my honeycomb here. Imagine you have a point here and you have some force over here. Let's call that f. And say, the force is at distance r from f. And say that it moves through some distance.
The moment here would be r times f. And if that rotates, say, through some angle-- let's call it alpha-- and here is f here, then this distance here that the force moves through is just r times alpha. So the work done is going to be r times alpha times f, or just the moment times alpha. OK? So that's all that we're doing.
OK. That's the internal plastic work. And now we have to look at the external work done. And that's equal to p times lambda over 2. Here, lambda is the half wavelength of the buckling.
I'm going to say for these tubular kinds of things, it's in the order of l. So if you look at that last slide here-- oops. Rats. How'd that happen? Let me scoot back down here.
There. If we look at that guy again, the magnitude of the buckling wavelength is on the order of l. And here, below p, can be related to the stress in the three direction. We'll just multiply it times the area of the unit cell.
And so if I equate the internal work and the external work, I can say p times lambda over 2 is equal to pi times my plastic moment. And then, for p, I can write sigma 3 h plus l sin theta times 2l cos theta. And then, lambda is l divided by 2 is equal to pi. And then I've got my plastic moment over there.
And then if I solve for sigma 3, that's my compressor strength. I've got pi by 4, the strength of the solid, sigma ys, times t over l squared. Then h over l plus 2 divided by h over l plus sin theta times cos theta.
And for the regular hexagons, this works out to about 2 sigma ys times to over l squared. And the exact calculation for regular honeycombs is equal to 5.6 times sigma ys times t over l to the 5/3 power. This power here-- 5/3-- is a little less than 2. And that's because the additional constraint of the neighboring cell walls.
But the main thing we're interested in, in these sorts of calculations, is the power dependence on the density and this simple calculation. Obviously, it's not exact, but it gets you close. OK. I'm just going to wait for people to catch up a little.
OK. The next property I'm going to look at is out-of-plane brittle fractures. Say we loaded in tension, and if we had no cracks in the walls, we'd just see uniaxial tension and the strength would just be the strength of the solid times the relative density times the amount of solid. We'll just say if defect free, the walls see uniaxial tension. And then the fracture stress in the three direction is just equal to the relative density times the fracture strength of the solid.
If the cell walls are cracked, and if the crack length is very much bigger than the cell length, then the crack propagates normal to x3. Then we can say the toughness gc-- or the critical strain energy release rate-- is just equal to the volume fraction of solid times gc for the solid.
And then the fracture toughness, k1c, is equal to the square root of the Young's modulus times gc. And that's just equal to the relative density times the modulus of the solid. And then the relative density times the toughness of the solid. So it's just equal to the relative density times the fracture toughness of the solid. It's just straightforward there.
Then we've got one last out-of-plane property. And that's brittle crushing and compression. And if we have some compressive strength of the cell wall-- say I call it cs-- then it's just the relative density times that strength. And for brittle materials, that crushing strength is typically around 12 times the modulus of rupture, or fracture strength. We could say that's about equal to 12 times the relative density times sigma fs, a fracture strength.
OK. That's the modeling of the honeycombs. I know there's been a lot of equations and derivations, but that's the basis of a lot of the things we're going to do in the rest of the course. The modeling we're going to do on the foams is based on this and the mathematics is just easier because we're going to use these dimensional arguments. We're not going to figure out all these geometrical parameters.
Before we get to the foams, I wanted to talk a little bit about honeycombs in nature. And we've only got a couple minutes left, so I won't really get that far. But I wanted to talk a little bit about honeycomb materials in nature.
And the two examples we're going to talk about are wood and cork. I'm going to talk a little bit about the structure of wood next time. Then, we'll see how we can apply these models to understanding how wood behaves. And we'll see how you can use these models to predict the density dependence of wood properties and also the anisotropy in wood properties.
And I guess we'll probably, maybe, start it Wednesday next week. We'll talk about cork, as well. Those of you who took 3032 know that I like cork because of Robert Hooke and his drawing of cork. And I made a new video that I'm going to show you. Remember in 3032, I showed you the video from the Bodleian Library, where they had the first edition of Hooke's Micrographia.
Well, it turns out Harvard has a first edition. Harvard has three first editions. Yeah. Exactly. MIT has zero first editions. Gee, why does that surprise me?
And I have a friend who's a librarian at Harvard and she arranged for me to go and make a little video with the first edition of Micrographia. So I can-- I don't if we'll play the whole thing, but I'll show you the first little bit of it. And you can watch it at your leisure.
And Sardar came. You came and saw it with me. You came and saw the first edition with me, right?
AUDIENCE: Yes.
LORNA GIBSON: Yeah. Yeah. It's very beautiful and you'll see some of the nice drawings. And I talk about the cellular structure of some of the drawings. So we'll talk about wood and cork next time. But I think I'm going to stop there because that seems like enough equations for now.
Free Downloads
Video
- iTunes U (MP4 - 164MB)
- Internet Archive (MP4 - 164MB)
Subtitle
- English - US (SRT)