Flash and JavaScript are required for this feature.
Download the video from iTunes U or the Internet Archive.
Description: This session covers wood structure, micro-structure, stress-strain, honeycomb models, and bending.
Instructor: Lorna Gibson
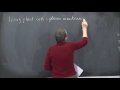
Lecture 6: Natural Honeycom...
The following content is provided under a Creative Commons license. Your support will help MIT OpenCourseWare continue to offer high-quality educational resources for free. To make a donation or view additional materials from hundreds of MIT courses, visit MIT OpenCourseWare at ocw.mit.edu.
LORNA GIBSON: So I should probably get started. So I just wanted to mention this Friday the libraries are having Furry Friday. So they have therapy dogs come, and if you like dogs, it's kind of fun to go get cuddled by the dog. The other thing I wanted to mention, last term, there was a student taking 3032 who was interested in art. And I kept trying to find art pictures for him, and he's not here. But I thought everybody else can like the art too.
So I belong to the Peabody Essex Museum in Salem, Mass. And they have an exhibit right now on wood and on sort of using wood as a sculptural material. And this is one of their posters to advertise it. So this thing was carved out of a single piece of wood, I think. And they've got lots of other sort of sculptural wood. So I thought you might like to see that.
If you wanted to go to Salem, there's a couple of options, if you don't have a car. You can take a commuter rail to Salem. You can also take the ferry. And if you take the ferry to Salem, it's like a five minute walk to where the ferry lets you off to get to the Peabody Essex. And it's a kind of neat museum. It's not too big. It's kind of small. But it's a beautiful building, and they have neat stuff there. So you could go to the Peabody Essex Museum. Hmm?
STUDENT: It's very nice.
LORNA GIBSON: Yeah, you've been there? Yeah, it's really nice. So I was going to talk about honeycomb-like materials in nature today. And I'm going to talk about wood today, and I might finish this today. I might not. And then I'm going to talk about cork for a little bit on Wednesday, and then we'll start talking about foams after that.
So I have a couple of sort of cute little language historically things. And you know how I like that stuff too. So I have two things about words that are related to wood. So the word "materials--" you know where the word materials comes from? It comes from the Latin. So there's a Latin "materies materia." And materies materia means "wood" or "the trunk of a tree."
So if you think of studying materials, in olden times that was like studying wood. And another cute thing that I found was that in old Irish the names of the first few letters of the alphabet are named after trees. So the letter A, that's called alem in old Irish, and alem is the word for elm. And B is-- I don't know if I'm saying these right. It's called beith, and that's the word for birch. And C is call. That's the word for hazel. And D is dair, and that's the word for oak. And so they sort of named the letters of the alphabet after different kinds of trees, different kinds of woods.
So I just thought those were kind of interesting historical things. So I wanted to start by talking about wood structure. And then we're going to look at how would deforms and fails, and talk about the data that people have measured for the wood properties, things like stiffness and strength. And then we'll talk a little bit about how the honeycomb models can be applied to understanding the mechanical properties of woods.
So this is kind of a generic trunk of the tree here. And we're defining three axes. The radial axis comes radially out of the tree. There's the tangential axis, so that's the x1 and the x2 axes. And then there's the longitudinal or the axial axis, x3. So if you think of the wood as being, in a very, very simple way, just like the honeycomb, the radial would be this way on. The tangent would be that way on. And that axial would be that way on.
So it's like that. And if you neglect the growth rings, you can say that other woods orthotropic, and that's typically what people do. They neglect the growth rings, and they say that it's orthotropic. And the density of the woods, the relative density ranges from about 5% for balsa wood to about 80% for lignum vitae.
So I brought in some pieces of wood. So this is balsa wood. You're probably familiar, making different kinds of models with balsa. So balsa's very light. It grows in Ecuador. And it's the lightest wood. And this is lignum vitae.
You're probably not so familiar with that. This actually grows in Florida, and it's the densest wood. It has a relative density of 0.8. And it's so dense, that if you put it in water, it sinks. So it's a very dense wood. And the way the wood cells grow is that if you look at the sort of structure here of a tree, there's the bark on the outside here, and then there's the kind of wood cells inside the bark. And there's a layer of cells in between the bark and the wood called cambial layer. And that's really the layer of cells that are alive and are dividing.
So if you think of the wood cells, they're living when they're in that little cambial layer there. And they're dividing. And that cambial layer, the cells have a plasma membrane and a protoplast. And then they sort of exude the plant cell wall. So a little like bone cells, like if you think of the bone in your body, there's osteoblasts and osteoclasis, different kinds of bone cells.
But the bone cells secrete the sort of collagen and the calcium phosphate that are the sort of hard mineral part of the bone that you think about in the bone. And that's not a living thing. The cells are the living thing. That's like an extracellular matrix.
In the trees, it's a little bit the same. So there's the living cells that are just under the bark, and they have this plasma membrane and the protoplasm. And over a few weeks they excrete the plant cell wall, and then they die. So the living cells die, and you're left with the plant cell walls. And then as the tree grows, you're always having a layer of these cambial cells, and it forms bark on the outside and wood on the inside.
So there's sort of a layer of cells that are differentiated, such that on the outer layer they form the bark, and on the inner layer they form the wood. And as the tree grows, that cambial layer is kind of expanding out radially. So let me write some of these things down.
Let's see. So let me just write down those two little word things because I think they're cute. So the word materials is from the Latin materies materia. And that means "wood" or the "trunk of a tree." And here's the little old Irish thing. It's not like I think-- I'm not going to put this on the test or something. I just thought it was cute.
So the letter A is alem, which is elm. And letter B is beith, which is birch. Letter C is call. That's hazel. And D was dair, and that's oak. So that's just for general interest.
So then the wood structure we can think of it as orthotropic, if we ignored the growth rings. And if you have a sort of large diameter tree and you take a piece of wood not from the very center, but from somewhere near the outside, then that's not a bad approximation. Now, the relative density of the woods ranges from about 0.05 for balsa to about 0.8 for lignum vitae.
Any Latin scholars here? I took one year of Latin in high school. Anybody take Latin? No, no Latin. So I think lignum vitae I think is "tree of life." "Vitae" is the sort of life. And when it has this ending A-E it means "of life." So I think that's the "tree of life" is lignum vitae.
So trees have cambial layer beneath the bark. And the cell division occurs in that cambial layer. So the new cells on the outer part turn into bark, and the new cells on the inner part turn into wood. And then we have the living plant cells that have the plasma membrane and the protoplast. And those cells then secret the plant cell wall, which sort of surrounds them.
So in trees, the living cells lay down the plant cell wall over a period of a few weeks. And then the living cells die. Oops. Back. Here. Now you always retain a layer of those cambial cells. So you may have heard if you have a tree and you cut a ring around the tree through the bark, if you go into those cambial cells and you destroy them, you kill the tree, because you're killing that layer of living cells.
So then we want to look at the cellular structure of the woods as well. And I've got a couple of slides here. This one is of softwoods. And softwoods have two types of cells. That have tracheids, which are the bulk of the cells here, and the tracheids provide structural support. And the tracheids also have little holes along the length of them at their ends called pits, and those pits allow fluid transport up and down the tree. And then the softwood also has these ray cells here. So those are examples of ray cells.
So this is a transverse section. This is a longitudinal section here. And the rays are parenchyma cells which store sugars. So softwoods have tracheids and rays. And then hardwoods, here's an example of a hardwood oak. They have three types of cells. There's cells called fibers, so these guys all in here would be fibers. They provide the structural support.
They have vessels, these really large cells that provide fluid transport up and down the tree. And they also have rays. So here are some rays here. And again, those rays are parenchyma cells that store sugars in the tree. So let me just write down what all these cells are.
So in softwoods most of the cells are these tracheids, so they make up the bulk of the tree, something like 90% of the tree. And they provide structural support. They have holes in the cell wall for fluid transport, and those are called pits. And to give you some idea of what size they are, they're are a few millimeters long, so something like 2 and 1/2 to seven millimeters long. And then they're tens of microns in the other two directions, so they're something like 20 to 80 microns across. And the cell wall thickness, t, is usually a few microns, so something between about two and seven microns. So typically, the denser the wood, the thicker the cell wall's going to be.
Whoops, let's see if I can get the rays down here. Put it on the same board. So the rays are parenchyma cells that store sugar. And then the hardwoods have three types of cells.
They have the fibers that provide the structural support. And the amount of cells that are fibers varies, depending on the species, but it's usually somewhere around 35% to 70% of the cells. And then they the vessels, which are the sap channels. That provides for the conduction of fluids. And that's between about 6% and 55% of the cells. And then, again, there's rays that store sugars, and they usually make a boat 10% to 30% of the cells.
So there's the structure of this sort of cellular structure, at this kind of length scale of tens of microns. And then there's also a structure within the cell wall itself. And the cell wall itself is made up of cellulose fibrils in a matrix of lignin and something called hemicellulose.
So if you look at the cellulose structure, the cellulose has a regular structure, a sort of periodic lattice. And it's crystalline for most of the length of the fibrils. So this is the structure of the cellulose here, and this is showing it at a slightly larger length scale. It might have a crystalline region here and then a non-crystalline region here. And these macro fibrils, which are made up of bundles of micro fibrils, are about 10 to 25 nanometers. And each one of the micro fibrils might be three to four nanometers across.
So you have these cellulose fibers. And then the cell wall is made up of different layers. So there's what's called the primary wall here, which has a random arrangement of the cellulose fibrils. Then there's an outer layer here. These are all called secondary layers. This is S-- I think that's S1. Yeah, it's S1. And it has this arrangement of the fibrils.
Then there's a layer called S2, and it's generally the thickest layer in the cell wall. And the cellulose fibrils are aligned not perfectly vertical, but a little off the vertical. And the angle between the vertical and the orientation of the cellulose fibers is called the microfibril angle. And then there's a third layer here, S3, with, again, a different winding of the fibers.
So because S2 layer is the thickest layer and because the fibrils are closest to the vertical axis, the S2 layer actually contributes the most to the longitudinal modulus and stiffness and strength of the cell wall. So that's kind of the arrangement of the cell wall. And then so that one cell would have that. Another cell would have that. And in between the two, there's a layer called the middle lamella that kind of glues them together. So that's the arrangement of the cells.
Let me scoot over here. So the cells are often modeled as a fiber reinforced composite that has four layers to it. And in each layer there's different volume fraction of the fibers and different orientation of the fibers. So the cell wall has this fiber-reinforced structure. Here's the cellulose fibers in a matrix of lignin and hemicellulose. And there's four layers, each with the fibers in a different orientation. And then there's the middle lemella between the two cells.
So in doing the modeling of a material like wood, you need to know what the properties of the cell wall material are, because, obviously, the properties of the wood would depend on the cell wall properties. And it turns out that they're similar. They're not exactly the same, but they're similar in different species of wood, so we're going to call them more or less the same.
So the density of the solid is 1,500 kilograms per cubic meter. The modulus of the solid in the axial direction is 35 gigapascals. The modulus in the tangential direction or transverse direction is 10 gigapascals. And the strength of the solid in the axial direction is 350 megapascals. And the strength of the transverse direction is about 135.
So here A means Axial direction, and T is transverse. And just for comparison, if you just look at cellulose, cellulose has some pretty amazing properties. The modulus of cellulose is about 140 gigapascals, which is very high for a polymer. And the strength of cellulose fibers run between about 700 and 900 megapascals. So the cellulose fibers have very impressive properties. And that's one of the things that gives wood very good properties.
So the next thing is I want to show you some stress-strain curves for wood. And you'll see how similar they are to the honeycombs that we looked at before. And then we'll look at how the cells are deforming as they're getting loaded. And from that, we're going to do some modeling.
So let me just wait till people get caught up. Are we caught up? More or less? OK. So these are all compression curves, so I'm just going to talk about compression. So these are curves for different types of woos. And on the left, the wood is loaded in the tangential direction. So in terms of the sort of honeycomb model, it's loading at kind of this way on, like that. And on the right, are a set of curves for wood load it in axial compression. So in axial compression loading, we're loading it that way on. And we've got different species here.
So the lowest density is balsa, around about 100 kilograms per cubic meter. The densest species on this plot is beech, which is around 700 kilograms per cubic meter. And then there's pine and willow, some other species in between here. So you can see the shapes of the curve look just like the curves that we had for the honeycombs.
So here there's a linear elastic bit. There's a stress plateau. And there's a densification bit. And then, as the density goes up, it gets stiffer, and the strain at which the densification occurs gets smaller, and the strength gets higher. And if we look at the axial properties, the shape of the curve is similar. We get linear elastic stress plateau densification.
But if you look at the scale here, this scale goes from 0 to 100, whereas that scale went from 0 to 20. And so the stiffness and the strength along the grain are much higher than they are across the grain. And you probably already know that. Wood is stronger and stiffer along the grain than across the grain. So that's what the stress-strain curves looked like. And the fact that we're getting the curves that look like that makes us think maybe the mechanisms of deformation and failure are similar to the honeycomb, too.
So here's a set of curves for balsa all plotted on the same scale. And, again, you can see for loading across the grain, either in the radial or the tangential direction, the stiffness and the strength is a lot less than if you load it in the axial direction. So a number of years ago, we had a project on balsa. And the thing we were interested in doing was looking at how the cells deformed and failed. And because balsa's a low-density wood, it was easier to see the deformation in the cells, because the cells were thin. So that's why we chose balsa.
I actually have a project on balsa right now. And [? Sardar ?], my postdoc, is doing more detailed kind of finite [INAUDIBLE] modeling, trying to represent the structure of balsa. And I think I mentioned, the reason we're interested in it is the balsa's used as a core in sandwich panels in wind turbine blades. It's actually the best material that they can find, it's better than any engineering material.
So that's comparing the three curves for balsa. And then if you look at a specimen that's loaded in the [? SCM ?], with a loading stage, you can measure the stress-strain curve, and you can take photographs of what the cellular structure looks like at different stages of loading. So here, this picture one, is unloaded. And these four images here are looking at the same section of cells, the same area of cells. And you can see there's a big vessel here, and that's the same vessel there.
So here, this image two, is at this point on the stress-strain curve. Here's three, at that point. And four is at that point. So if you look at this carefully-- and I've got another higher mag picture I'll show you in a second-- you can see that what's happening is the cell walls are bending. So it's kind of like taking my honeycomb like this, and I'm doing that to it, and the cell walls are bending, so just the same as the honeycomb. And then eventually, if I load it enough, you get to this sort of densified stage. And you're doing this, and the stress-strain curve increases sharply.
So here you can see how the cells have densified over here. It kind of looks a lot like my honeycomb when I-- maybe I do it this way-- when I smush it up like that. It looks kind of similar. So if we look at the higher mag picture, again, these four images are the same area of the cells. And if you look at that a little bit of crud, it's the same on all four of them there.
So this is the unloaded one. And these were loaded from top to bottom. And this is loaded to some extent/ that's loaded more, and that's loaded more. So if you look at this cell here, it's got this little tear on it. So you can sort of find it again. If you look at that cell there, that's what it looks like unloaded. And here you can see-- see that wall there? You can see how it's bent up.
So it's bent like the honeycomb walls. And here it's bent even more. And eventually, it has this sort of a shape here, and it's deformed permanently. It's formed one of these plastic hinges. So it's like the aluminum honeycombs almost, that it's filled like that. So in the balsa wood, when we load it in the tangential direction, we're getting bending of the cell walls and then yielding and plastic hinges forming, just the same as we would in an aluminum honeycomb.
Are we good with that? Well, I'll go through all three directions. And then I'll write down the notes. So this is loading the balsa in the radial direction. And these things here are the rays. So we're loading it in that direction. And here you see this also bending occurs, but the rays act a little bit like fiber reinforcement. So the rays are a little bit stiffer, and they sort of reinforce the thing a bit. And this is the loading platten here, and you can kind of see that the failure starts at the loading platten, and as you sort of load up more, it progresses in from the loading platten.
So we're going to look at the modeling of the balsa in the radial direction, and we're going to count for the rays, at least in a crude way. And then when you load them balsa in the axial direction, initially you don't really see much happening. So if one is unloaded, one's down here. And two is at this peak stress up here. And really, if you look between one and two, you just don't see an awful lot of difference. And that's because what you're doing is you're taking the wood and you're loading it this way on. And it's so stiff, you just don't see much deformation. So there's not really much to see.
But then eventually, something starts to fail. And in this case, what fails are the end caps. So the balsa wood has these long cells here. But then at the end of the cells, there's little caps on the ends. And the cells kind of fit together like that. So that eventually, if you keep smushing it, those end caps start to fail.
Here you can see how bright it gets, and the cells are starting to crush together and kind of fail those end caps. And in fact, each one of these serrations here, if you look at, say, from that peak up to that peak, that corresponds to a length of about the length of the cell, or the length of the cell between the end caps. So in axial deformation you're just actually deforming the cells until you break those end caps.
If you look at denser words, they fail in slightly different ways. This is a Douglas fir, which is much denser. This particular specimen, the whole thing is kind of buckled over. So it's not really so representative of the structure itself. This is Douglas fir in radial compression. You can see this picture, it looks just like what I showed you for the balsa wood, that sort of propagation of the failure. These long things here are the rays.
And this is a Norway spruce in axial compression. And this is fairly common in denser words. You get this buckling formation. And what happens is, I think, you get some yielding of the cell walls initially, but that leads to buckling, like a plastic buckling. And you can see on this higher mag picture down here, you get these really small wavelength buckles in the cell wall. And the two-- you get a plane that kind of shears over itself. And you can see in the top image, this top half has shared over relative to the bottom half. And all the deformation is in this little band here. So this stuff here is all going on in that band up there.
So let me write down some notes about how these things to form and fail. And then we'll get to the modeling in little bit. So we can say the stress-strain curves resemble those for honeycombs. And I'll say the mechanisms of deformation and failure are most easily identified in low density balsa wood. So for balsa, if we look at the tangential loading, we see bending of the cell walls and then eventually plastic yielding.
And for radial loading, the rays act as reinforcing. And for axial loading, you get axial deformation and then the failure of the end caps. And I'll just say failure by plastic buckling is also observed, say, in the denser woods.
[INAUDIBLE]
So then we can look at some data for the properties of woods. And these charts plot relative Young's modulus and relative strength against relative density. So here the modulus of the wood is divided by the modulus of the solid cell wall material. And here we've normalized everything by the modulus of the solid cell wall material in the axial direction, because the cell wall itself is anisotropic. And so here's the relative modulus, and here's the relative density.
These are log-log plots. And we see that when we load the wood in the axial direction, the moduli is just linearly related to the density. And when we load it across the grain, it varies with the cube of the relative density. So do you remember our little honeycomb models?
If I took the honeycomb and I loaded it this way, it went as the cube of T over L. And that's because the bending. And so the wood doesn't lie perfectly on that cube line, but it's fairly close. And then similarly, if we took the honeycomb and we loaded it this way on, it deformed axially. The modulus depended linearly on the density.
So you get the same kind of relationships there. And then if you look at the strength, the strength along the grain goes linearly, and the strength across the grain goes with the square. And we'll see when we get to the modeling in a minute, that if we loaded, say, an aluminum honeycomb this way on, the strength would go linearly with the density, if we're just yielding the cell walls. And if we loaded it this way on, it went as the square of T over L. So these things kind of correspond.
And you can see the structure of the wood is a lot more complicated than just a simple honeycomb. And so these models are sort of first order, and they're fairly crude. They don't try to capture every detail of the wood structure. But they can give you a sense of where the wood properties are coming from.
So let me just write down some of these observations. So the data for the wood-- the modulus along the grain goes linearly with density. It goes more or less as the cube for loading in the tangential direction. And the radial direction is somewhat stiffer different than that.
The strength in the axial direction goes linearly with the density. And the strength across the grain goes with the square of the density. And then there's data for the Poisson's ratios too. So let me just write them down.
So the modeling based on the honeycomb is sort of a simplified model that gives you kind of a first-order description of the behavior. And it doesn't really attempt to capture all the details of the softwood and hardwood structure. And in the equations, I'm going to take the cell wall properties along the grain, or along the axial direction. And we're going to have a bunch of constants that describe the cell geometry, and those constants are also going to reflect the cell wall anisotropy.
So we can model the wood structure as something that's a bit more of a simplified thing, just like this. And we say we've got cells that are roughly hexagonal, and then we've got some cells that are more or less rectangular that are the ray cells. And if you look at lots of micrographs, you can get some idea what the dimensions of the cells are. And these dimensions were measured for a particular density of balsa wood.
So if we look at the linear elastic moduli, we can start off with a tangential loading. And if we have the tangential loading, we can model it as a honeycomb loaded in the plane, and we get cell wall bending. And from the cell wall bending in the honeycomb model, you would get that the tangential modulus varies with the relative density cubed. And the structure's not quite that simple.
There's ray cells. There's end caps. And they act to stiffen it a little bit. And the data lie a little bit above this line. Then if we look at the radial loading, the rays kind of line up with the radial direction, and the rays act as reinforcing plates. And so you can just use kind of an upper-bound composites idea to get the modulus. And the rays tend to be a bit denser than the fibers.
So if I say a Vr is the volume fraction of rays, and R is the ratio of the relative density of the rays compared to the fibers, so it's rho over rho S for the rays divided by rho over rho S for the fibers. And that varies a little bit from what one species to another, one specimen to another. But it's something a little over 1, something between 1 and 2.
Then I can say the modulus in the radial direction is the volume fraction of the rays times R cubed times the tangential modulus plus 1 minus the volume fraction of rays times the tangential modulus. And that works out to be about 1.5 times the tangential modulus. I wanted to work this out in terms of the tangential modululs, so I've put this in terms of the tangential modules in the first term there.
So we get that the radial modulus is slightly larger than the tangential, but also goes roughly as the cube of the density. And then for the axial loading, we just have axial deformation in the cell wall. And the Young's modulus just varies linearly with the density.
So these are kind of simple models, but they kind of explain to first order the density dependence of the wood moduli and the anisotropy. So it's kind of nice because they're fairly simple models, and it gives you kind of a big picture. So if you wanted to know the modulus of a particular piece of wood, this probably isn't the best way to figure it out.
But if you wanted to kind of compare how do woods behave in general and how does the density affect the properties and why are they anisotropic, this is a pretty good way to do it.
We could also look at the Poisson's ratios. And just because I didn't want to write them down again, I've just left on what the data were down here. But let me just write what the model would give us for nu RT and nu TR, the model would give us one if we had regular hexagonal cells. And these are the values we get here. This might be 0.6, 0.7 would be a typical value, somewhere around 0.4 in there, so they're not quite one, but they're close to it. And I think the reason they're a little less is because the rays in the end caps provide some constraint.
If you have the honeycomb, if I just had these cells, and I squeeze it like this, these guys can move out. If it's a regular hexagonal honeycomb, the strain that I'm applying here is equal to the strain going out that way. But if I have rays this way that sort of constrain it or end caps, it means that the Poisson's ratio is going to be a little bit less.
So I'll just say constraining effect of the end caps and rays-- constraining. Then for nu RA and nu TA, the model says the value we would get would be zero. And these are pretty close to zero. They're not quite zero, but pretty close. And then the last pair nu AR and nu AT, the model says that we would get nu of the solid. And the data's close to 0.4, which we might expect would be about the nu of the solid.
So, again, there's some variation in the Poisson's ratios. They're not all just one number. But you can see these ones here are about zero, and that's roughly what the model says. These ones here are closer to 1. And then these ones here are closer to what you might expect for a solid material. So it gives you the kind of general idea.
Are we good? We're good, yeah?
So we can do a similar thing for the compressive strength. So for tangential loading, we get plastic hinges forming and the bent cell walls, just like in an aluminum honeycomb. Then we get that the strength over the cell wall strength goes as the relative density squared, so just like the honeycomb.
the radial loading, we can do the composites thing again. So we can say the strengths in the radial direction is about equal to the volume fraction of rays times R squared times the tangential strength plus 1 minus the volume fraction of rays times the tangential strength. And for balsa, I have some values here. VR is about equal to 0.14. R is about equal to 2. And so the radial strength is about equal to 1.4 times the tangential. And in higher density woods, the value of R is a little bit smaller, and in general, the radial strength is a bit larger than the tangential, and both depend on the density squared And then for axial loading, if the failure's initiated by yielding in the cell walls, then the axial strength's just going to depend linearly on the density.
So the idea with these models isn't that they kind of describe a particular piece of wood exactly. It's more that it gives you a general picture of how the cells are deforming and failing, and how the properties scale with density and why the wood's anisotropic.
Are we good? Yeah? Caught up. So there are a couple more sort of interesting things we can do with looking at the wood properties. So we've been talking about how to model the cellular structure. But people have also looked at how to model the cell wall as a fiber composite. And this plot and the next one kind of show you how you can combine all of that together.
So remember, I said the modulus of the cellulose was around 140 gigapascals. So here's the modulus of the cellulose, at least the crystalline part of the cellulose plotted in that little envelope there. The lignin and the hemicellulose have a modulus around 2 or 3 gigapascals, so it's down there. And if you made composites with cellulose fibers in lignin and hemicellulose matrix, those composites would have a modulus that fell in this envelope here.
They've got to be in between those two limits, right? The modulus have to be between those two limits. The density have to be within the densities of the constituents. And if you look at the modulus of the wood cell wall, it lies in this envelope here. Along the grain it'd be here, and then across the grain is further down here.
So the cell wall modulus is in here. And then if you take that cell wall and you make it into the honeycomb-type material that wood is, if you load it along the grain, you're going to get this linear dependence of modulus on density. And if you load it across the grain in the radial or the tangential direction, you're going to get this cubed dependence here.
So here's a set of data for different woods of different densities. And that envelope kind of encompasses all of them. But if you look at the slope of that data, it's roughly equal to a slope of 1. And so it corresponds to that equation there. And similarly, here's a set of data for different species of woods of different densities loaded perpendicular to the grain. And they lie on a line that has more or less a slope of 3. And this set of data here along the grain intersects the wood cell wall towards the top of that envelope, and this set of data here intersects closer to the bottom of that envelope for the cell wall material.
So this gives you a way of sort of putting everything together on one plot-- the cell wall as well as the cellular structure. So that plot does it for the modulus. And you can do the same kind of thing for the strength. Here's the cellulose up here. Here's the lignin down there. Here's the wood cell wall, the composite made from those two. And then here's data for different kinds of woods loaded along the grain and for load across the grain.
So it gives you a way of putting all this modeling into one set of plots. So let me just write a couple of little things about that. So we could say you could model the cell wall as a fiber composite. And you can use the composition upper and lower bounds to give an envelope. And then you can also show the cellular solids models on the same plot. So overall, it shows you how the hierarchical structure fits together and can be modeled.
Now there's some more cute things we can see. So another thing I want to talk about is material selection, because it turns out wood is very good compared to other materials in certain applications. So we're going to look at, say, having a beam of a given stiffness at a given span, and say it's just a square cross-section beam of edge length T. And the question is, what material would minimize the mass of the beam?
So say we have some span we have to have. It's got to have some rectangular cross-section, some given stiffness. And the question is, what's the material that minimizes the mass? So there's a little short calculation we can do to figure that out. And then I've got another plot, and you can compare different materials on this other plot. Then you'll see how good wood is compared to other materials.
So from beam of a given stiffness and given span, and say it's a square cross-section, then the question is, what material minimizes the mass of the beam? So the mass is just going to be the density times t squared times l And if it's a beam, say it's got some central load on it, a concentrated load, the deflection's going to go as pl cubed divided by some constant and divided by the Young's modulus and the moment of inertia I.
So the stiffness, if I just rearrange this, the stiffness, p over delta, that's going to go as p over delta CEI, and I's going to go as t to the fourth over l cubed. And then I can solve that for t squared. And I want t squared because I'm going to plug it back into the equation for the mass.
So if I solve this for t squared, I've got my stiffness p over delta. I've got l cubed divided by CE. And then I take that whole thing to the 1/2 power like that. And then I plug the t squared back into the little equation for the mass. So I've got density minus p over delta times l cubed over CE. And we'll take that whole thing to the 1/2 power-- [INAUDIBLE] another l.
And so to minimize the mass, you want to look at the material properties. And here, the material properties are the density and the Young's modulus. And to minimize the mass, you want to minimize rho over E the 1/2 power. Or conversely, you want to maximize E to the 1/2 over rho.
So if you just had a bar that you were just pulling on, you would just want to maximize E over rho. But if it's a beam and bending, it works out that you want to maximize E to the 1/2 over rho. And if we look at the next slide, this next slide then plots on a log-log scale, it plots the modulus on this axis and the density on that axis. And here this plotted data for lots of different materials.
So there's engineering alloys. Metals are up here. Engineering ceramics are here. Composites are here. Polymers are down here. Elastomer is way down here. Foamy things, down here. And this envelope here is woods. And notice log scale here. The lowest stiffness polymer foams here are 0.1 gigapascal, and diamond is up here at 1,000 gigapascal. So there's like five orders of magnitude difference in the modulus here.
So then, if you look at the bottom right corner here, there's a bunch of old dashed lines. And this red one here is E to the 1/2 over rho. So if it's log-log plot, E to the 1/2 over rho's going to show up as a straight line. And every point on that line has the same value of E to the 1/2 over rho. And the material that would be the best for a beam of a given stiffness would be the one that has the biggest value of E to the 1/2 over rho.
And if I move the line up to the top left here, I'm increasing E. I'm decreasing rho. It's got the biggest value of E to the 1/2 over rho. So the materials that are on this line here, they all have the same value of E to the 1/2 over rho. And they've got the biggest value-- well, virtually the biggest value.
So let's look at what those materials are. There's things like engineering ceramics, like diamond that maybe are not the most convenient thing to make our beam out of, and tend to be brittle and might break. So we have some issues. There's engineering composite, so things like carbon fiber reinforced plastics. And at this sort of tip of the composites, there'd be things like unidirectional fiber composites. And then here's other woods down here.
So the woods have the same performance index, this is called, the same value of E to the 1/2 over rho as the best engineering composites. And so they have very good properties for their weight. And one of the interesting things is if you look at this performance index of E to the 1/2 over rho, this is the performance index for the wood. This is for the solid cell wall material that the wood's made from, so E to the 1/2 of the solid over rho for the solid. And from the modeling of the wood, just looking at the axial modulus, this thing here is equal to that times rho S over rho.
So if you look at this, this is the performance index for the wood. This is the solid it's made from. This number here is bigger than 1, right? Because the density of the solid is bigger than the density of the wood, and so this is saying the wood is more efficient than the thing that it's made from, than the solid that it's made from. And so that's the sort of plot for the stiffness. And there's a similar plot for the strength.
That if you do the same little kind of calculation, you find that the performance index for the strength is some failure strength raised to the 2/3 power over a rho. And again, here we're plotting strength versus density on a log-log plot. And this red line here is the strength of the 2/3 over rho. And again, if we scoot over here so we have a parallel line, every point on that line has the same value of the strength to the 2/3 power over the density. And these are the materials that have the highest values.
And again, here's engineering composites. These are ceramics. But the ceramics, they have a high compressive strength, but they tend to be brittle. So it's not really a practical strength. These are metals in here. And here's the woods down here.
So it's kind interesting just to see that the wood has such a good property. Yes?
STUDENT: So I realize why this is valuable setting up the problem this way. But if you're actually trying to design something, why would you want to fix your cross-section? You could change your material and change your cross-section.
LORNA GIBSON: So this is the starter version of this problem. And there's another part two of the problem is to change the shape. And you could look at what shape's efficient. There's something called a shape factor that gives you the efficient shapes. So you could take the material and turn it into a different shape and have a more efficient thing because it was a different shape. So you can account for that.
STUDENT: So then if you varied, like let's say you made your cross-section smaller, like even if it was still square, you could just still make it smaller.
LORNA GIBSON: Yeah. I'm saying we've got a given stiffness. So if we're given a certain stiffness and a certain span, we would need a certain cross-section to get to that stiffness. Are we happy? OK.
So that's one thing. Let's see here. So let me just write a few more notes about the material selection, and then there's one more thing I wanted to show you about the woods. Hmm? C is just a constant. So it's just a number. So if you had a beam in three-point bending, then C would be three. If you had a beam that was simply supported with a central load, C would be 48. C is just a number.
STUDENT: One more question. So follow your line there, and the choice is really just about cost.
LORNA GIBSON: No, it's not about cost. There's nothing on cost here. It's all really about the properties. What's the best combination of properties to minimize the mass, and then which material has that combination of properties. You can do charts like this that include cost. You can make these charts with whatever property.
STUDENT: [INAUDIBLE]. I guess maybe there's a difference off two or so of strength.
LORNA GIBSON: Between pine and balsa? Yeah, maybe more than that. I think-- I can't quite see where-- pine's close to 100, and balsa's, I don't know, 20 or something.
STUDENT: [INAUDIBLE]
LORNA GIBSON: Yeah, and it's not-- the point of this isn't so much looking at the absolute value of a strength. It's looking at the value of this performance index. And what you want to do is maximize that index to get the material that's going to minimize the mass. So let me just read a couple notes about this.
So we have these-- these are called material selection charts. So you plot the log of one property versus the log of some other property. And then we have a line of constant E to the 1/2 over rho. I'll just say it's shown in red because you're going have the same plots. And the materials with the largest values are in the upper left. So the woods have similar values to engineering composites. And you can do a similar thing for strength.
So I have a few more minutes. So I have a few minutes, and I want to talk about a couple of uses of woods. So one is in old ships. So I don't know if you know Professor Lechtman has this course Materials and the Human Experience, and they talk about sort of ancient uses of materials. And I did a section, a module, on woods and the use of woods in old colonial ships, like The Constitution that's in Boston Harbor.
So this is kind of a schematic of an old ship. And the thing that was interesting and the thing I talked about in this module was that people chose particular species for particular parts of the boat. And they would choose a particular species depending on its properties. And a lot of the hull was made of oak. So oak's a very dense wood.
But they would get something they called straight oak, and they would get something they called compass oak. And you can see this little thing down here, this little kind of schematic here, this little sketch. This is straight oak, just a straight trunk. And this thing here would be the compass oak. And what they would do is they would use the straight oak for straight parts of the boat, so something like this, these pieces here. And then they would actually look for trees that had the curve of the branches to match some part of the boat that they were looking for.
So, for instance, if you have the hull out here and the deck here and they had their cannons here, there's something called a knee, which is sort of a bracing piece that goes between the deck and the hull. And that bracing piece is curved. And they would actually look for trees in which the branches curved at the same kind of curvature as they were looking for in that piece. And then they would use it for that piece. And the advantage of this is they basically had the grain running along the curve, and so they got the best properties out of the wood by doing that.
So they had this straight oak and compass oak, and that was one cute thing. And often they used white oaks. And I brought a piece of white oak in. You can see how dense it is. And the US Navy often used something called live oak. Live Oak grows in the South. Anybody from the South? You see these big trees with huge sort of spreading branches. Those are the live oaks. And apparently, the US Navy, I read somewhere, still has a forest somewhere with live oak for doing things like repairing The Constitution.
So let me just pass those guys around. So those are a couple of oaks they would use for the hull. Then they would use white pine for the masts. And the reason they used white pine for the mast is because the white pine grows very, very tall and very straight. And white pine was actually like a strategic resource in the 1600s, the 1700s.
And it turns out that when the British Royal Navy was doing all that colonial stuff in the 1600 and 1700s, Britain actually ran out of trees for masts for boats, and they would actually import masts from New England. And there were these people called surveyors who would go around and they would mark certain trees that were supposed to be saved for these masts for the British Royal Navy. And the thing was that the size of the boat and how many cannons you could put on the boat depended on how big the mast was.
So the size of the boat depended on the mast, because the mast height controlled how much sail area you could get. So the taller the mast, the more sail/ the more sail, the bigger the ship. The bigger the ship, the more cannons. And so having these tall Eastern white pines was a sort of a strategic resource. And I have a piece of white pine.
Unfortunately, my dog got to this one. And be careful. It's a bit splintery. But you can see it's a lighter kind of wood. And if you go around New England, if you go to the arboretum, you can see white oak. You can see Eastern white pine.
The other wood they used is lignum vitae, that first dense one that I passed around. And if you notice that lignum vitae has kind of a waxy feel to it. And they used that in the block and tackle, so like pulleys and stuff like that. And it was thought to be self-lubricating because of that kind of waxy layer on it. And because it's very dense, if you think of like a block and tackle and you've got like a rope going over a pulley, you've got a pressure from everything sort of fitting together and the bits bearing against each other. And the fact that was very dense made it very good for the block and tackle. And so they used the lignum vitae for that.
And there's one other cute story about lignum vitae. I don't know if any of you've ever read Dava Sobel's Longitude. Anybody read that? I'm a sucker for those history of science books. So her book Longitude is about the development of an instrument to measure longitude.
Originally, they could get the latitude from the stars, but they were really bad at getting the longitude. And so boats would go off, and they wouldn't really be able to figure out where they were, until they had a method to measure longitude. And there was some British board of something or another.
They put forward a prize for somebody who could produce a way of measuring longitude accurately. And there was a guy called John Harrison, and he built a clock. He built a very accurate chronometer. And if you knew when sunrise was and sunset was, and you knew the time and where you left, you could figure out where you-- it's kind of like time zones. You could figure out where you are today. And he built a chronometer, and one version of his chronometer used a lignum vitae for the same reason, because it was very dense, and it was very stable.
And the clock that he eventually won the prize with was in the 1700s, 1759. I think they went on some trip with it. It was 81 days at sea, and it lost five seconds over 81 days. So that's pretty impressive for 250 years ago. So that was the lignum vitae in the clock.
I have one more picture, and then I can finish up the thing on wood. And we'll start the cork next time. So this is another example of using wood. And this is sort of a more modern use. So this bridge here is made with a glue-laminated wood.
So this big beam here, the big arch, is made up of sections of wood which are glued together. And you can glue the sections in a curved shape if you want. They sort of have molds to do that. And when they make this glue-laminated wood, they cut the defects out. So they cut knots out, and they control the pieces of each laminate that they use to get the best quality. And the glue-laminated wood actually has better properties than just two-by-fours or whatever you would cut down, lumber that you would cut from a tree.
So glue-laminated wood is kind of a nice kind of wood structure that's used now. And you see it all the time in things like ice rink arenas, like large spans. It's kind of beautiful. You can see the wood grain in the curve in the wood grain when they make these things. So that's the wood lecture.
I'm going to stop there. So next time I'll talk about cork. I just have a little bit about cork. And then we'll start talking about foams.
Free Downloads
Video
- iTunes U (MP4 - 175MB)
- Internet Archive (MP4 - 175MB)
Subtitle
- English - US (SRT)