Flash and JavaScript are required for this feature.
Download the video from iTunes U or the Internet Archive.
Description: This session includes a review of honeycombs, and explores the mechanical properties of honeycombs.
Instructor: Lorna Gibson
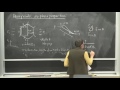
Lecture 4: Honeycombs: In-p...
The following content is provided under a Creative Commons license. Your support will help MIT OpenCourseWare continue to offer high-quality educational resources for free. To make a donation or view additional materials from hundreds of MIT courses, visit MIT OpenCourseWare at ocw.mit.edu.
LORNA GIBSON: OK, so it's five after. We should probably start. So last time we were talking about honeycombs, and I just wanted to quickly kind of review what we had talked about, and then today I'm going to start deriving equations for the mechanical properties of the honeycombs, OK? So this is a slide of our honeycomb setup here. These are the hexagonal cells we're going to look at. We talked about the stress-strain behavior. The curves on the left-hand side are for compression and the ones on the right-hand side are for tension.
And so what we're going to be doing today is we're going to start out by calculating a Young's modulus, this slope here. We're going to calculate the stress plateaus for failure by elastic buckling in elastomeric honeycombs, by failure from plastic yielding in, say, a metal honeycomb, and by failure by a brittle crushing in, say, a ceramic honeycomb. And if we have time, we'll get to the tension stuff. I don't know if we'll get to that today or next time.
So we're going to start calculating those properties today. And these were the deformation mechanisms. Remember, we said the linear elastic behavior was related to bending of the cell walls, and then the plateau was related to buckling if it was an elastomer. And the plateau was related to yielding if it was, say, a metal that had a yield point. And then this was sort of an overview of the stress-strain curve showing those different regions, OK?
So what I'm going to talk about today to start is the linear elastic behavior. And we're going to be starting with the in-plane behavior. So in-plane means in the plane of the hexagonal cells. And then next time we'll do the out-of-plane behavior, this way on. So if I had to form my little honeycomb like this, what initially happens is the inclined cell walls bend.
So if you can see over here, we've kind of exaggerated it on this sketch. So this wall here is bent. This one here just kind of moves along, goes for the ride. And this guy here is bent. So this is for loading in the what we're calling the x1 direction, sigma 1. And the same kind of thing happens when we load in the other direction, in the sigma 2 direction, these guys still bend. Now the honeycomb gets wider that way. It gets shorter this way, wider that way.
And we can calculate the Young's modulus if we can relate the load on the beam in the moments to this deflection here, right? So the Young's modulus is going to be related to the stiffness and the stiffness is going to be related to how much deformation you get for a certain amount of load that you put on the beam. So I'm going to calculate the modulus for the x1 direction, the thing on the left there. And you can do the same thing for the x2 direction on the right, but I won't calculate that because it's exactly the same kind of process.
OK, so let me start here. Get my chalk. So I'm going to draw a one-unit cell here. So here's my unit cell there, like that. And this member here is of length h. That member there is of length l. That angle there is theta. I'm going to say all the walls have equal thickness, and I'm going to call it t. And I'm going to define an x1 and x2 axis like this. So the horizontal is x1 and the vertical axis is x2.
And I'm going to say that I apply a sort of global stress to it, sigma 1. So there's a stress in the one direction there, sigma 1, OK? And I'm going to say my honeycomb has a depth b into the page, but the depth s-- is because the honeycomb's prismatic, the b's are always going to cancel out of all the equations that we're going to get, because everything's uniform in that direction.
And we can think about a unit cell here, and in the x1 direction, we could say the length of our unit cell is 2l cos theta. So in the x1 direction, that's our unit cell there, and that's 2l cos of theta. And in the x2 direction, you might think that you go from this vertex up here down to that vertex there, but if you did that, then on the next layer of cells, you wouldn't have the same distance.
So the unit length in the x2 direction is actually from here to here, and then you can see the next cell, you would get the same thing. You get this bit here from the inclined member, and then you would get h down here from the next member. So this bit here is equal to h plus l times sine of theta. So I can say in the x2 direction, the length of the unit cell is h plus l sine theta, OK?
So that's kind of the setup. And then what we want to look at is that inclined member that bends, we want to look at how this guy bends under the load. And if we can relate the forces on it to the deflection, and we need the component of the deflection in the one direction, then we're going to be able to get the modulus. So I'm going to draw that inclined member again over here, and it's going to see some loads that I'm going to call p, and that's going to cause this thing to bend.
So I've kind of exaggerated it there, but there's the bending. And there's some end deflection there, delta. And there's moments at either end of the beam, or either end of that member, as well. And this member here has a length. That length is l. OK, are we good? So it's just kind of the setup. And I'm going to draw the deflection delta bigger over here. So say that's delta. That's the same parallel as this guy here. What I'm going to want is the deflection in the x1 direction, and when I come to calculate the Poisson's ratio, I'm going to want the deflection in the x2 direction. And if this angle here is theta, between the horizontal and the inclined member, then this angle up here is also theta, and so this bit here is delta sine theta. And this bit here is delta cos theta. Ba-doop-ba-doop-ba-doop.
So the Young's modulus is going to be the stress in the one direction divided by the strain in the one direction. So I need to get the stress and the strain in the one direction. So here the stress in the one direction. If I'm applying my load, like this, sigma 1, the stress in the one direction is going to be this load p-- so this load, say, p on this member here, divided by this length here, the unit cell length, and then divided by b into the board, the width end of the board.
So sigma 1 is going to be p divided by h plus l sine theta times b. And epsilon 1 is going to be the strain in the one direction, is going to be the deformation in the one direction divided by the unit cell length in the one direction. So that's going to be delta sine theta divided by l cos theta. So here, even though I've said this unit cell is 2l cos theta, there'd be two of the members here that would be twice that deflection in the one direction.
So it's, for one beam, it's delta sine theta over l cos theta. Are we OK so far? So far so good? So for the hexagons, because we're going to figure out the equations more or less exactly, we're going to keep track of all the geometrical factors. When we come to the foams, we're not going to keep track of all the geometrical factors. So one of the things that makes us look a little kind of hairy is just the fact that we're keeping track of all these sines and cosines and all the dimensions and things.
All right, whoop. So I need to be able to relate my load p to my deformation delta to get a stiffness out of this, to get a modulus, OK? So the way I do that is, remember in 3032, we did those bending moment diagrams and we did the deflection of the beams? This is where this comes in handy. So I'm going to draw my beam a little bit differently now. I'm going to turn it on its side. So this is still my length l, but I'm going to turn on my side just so that you can see it the same kind of way we did the bending moment diagrams.
So this is still my length l across here. And there's end moments, M and M here. And P sin theta is just the perpendicular component of the load p. So p sin theta is just the component perpendicular to my beam.
So I could draw a shear diagram here and I could draw a bending moment diagram here. And, if you remember, the shear diagram, if I have no concentrated load along here, and I have no distributed load along here, if this is zero, down here, it's just going to go up my P sin theta, and then be horizontal, and then come down by P sin theta, OK? So that's the shear diagram.
And then the bending moment diagram, I'm going to draw down here. So I've got some moment at the end here, and this would tend to bend like that. So this would be a negative moment. Remember, bending moments were negative if there was tension on the top, and they were positive if there was tension on the bottom. So over here we'd have tension on the top, so that would give us a negative bending moment.
And then, if you also remember, the moment at a particular point is equal to the integral from, say, A to B-- well maybe I should write this another way. And B minus Ma is the integral of the shear diagram between the two points. A little sloppy. OK. So if I know how I have some moment here minus M, if I integrate this shear diagram up, then this is just going to be linear here, and then I'm going to be at plus M over there.
So if you look at this shear and bending moment diagram, it's really just the same as the shear and bending moment diagram for two cantilevers that are attached to each other. So let me just draw over here what the cantilever looks like. Let's see. So imagine I just had a cantilever like this, and I have some force F on it like that. And I call this distance here capital L, and I'm going to call that deflection capital delta, like that.
If I drew the shear diagram for that, there'd be a reaction here, F, there would be a moment here, FL. Doot, doot, yup. So this would look-- whoops-- it's a little too long. Shear diagram here would look like this. That would be zero. This would be FL. And the moment diagram would look like this. Whoops. A little too long again. And that would be minus FL. And that would be zero.
So do you see how the shear and the bending moment diagram here are really just like two cantilevers, OK? So I know that the deflection for a cantilever, delta, is equal to F capital L cubed over 3EI. It's kind of a standard result. And so I can take this and apply that to this beam here. So instead of working everything out from first principles, I'm just going to say that my beam here is like two cantilevers, and instead of F, I've got P sin theta. And instead of capital L here as the length, I've got l/2 because l/2 would be the length of one of the cantilevers.
OK, so for the honeycomb, I've got two cantilevers of length l/2. So delta for the inclined member on the honeycomb is going to be 2-- because I've got two cantilevers-- the force, instead of having F, I'm going to have P sin theta. And instead of having capital L, I'm going to have l/2, all cubed. So this is like F capital L cubed over 3. And here, the modulus that I want is the modulus of the solid cell wall material, so I'm going to call that ES, and over the moment of inertia. So you see how I've done it? Is that OK?
So then I can just kind of simplify this thing here. I've got P sin theta l cubed. 1/2 cubed is going to be 1/8. So this is going to be 2, if that's 1/8, times 3 is 24. So 2/24 is 12. So I've got delta for my honeycomb member is P sin theta l cubed over 12 EsI. And here I is the moment of inertia of that inclined member of the honeycomb. And that's BT cubed over 12, OK?
So B is the depth into the board, and T is the thickness. We'll cube that and divide by 12. It's a rectangular section. Yeah?
AUDIENCE: What was ES again?
LORNA GIBSON: ES is the Young's modulus of the solid that it's made from. So clearly, if my honeycomb is made up of these members, whatever material the members are made of is going to affect the stiffness of the whole thing. Are we good? Because once we have this part, then we just combine these equations for the stress and the strain in the one direction. And we have this equation relating delta and P, and we're going to be able to get our Young's modulus, OK? We're happy? OK. All right.
So I'm going to call the Young's modulus in the one direction E star 1. So everything with a star refers to a cellular solid property, and 1 because it's in one direction. So that's going to be sigma 1 over epsilon 1. So if I go back up there, I can say sigma 1 is equal to P divided by h plus l sin theta b. And epsilon 1 is equal to delta sine theta in the denominator over l cos theta.
And now instead of having delta here, I can substitute this thing here in for delta. And then I'm going to able to cancel the P's out. So delta was equal to P sine theta l cubed over 12 Es, and there was an I, a moment of inertia, and I was equal to bt cubed over 12.
And let's see here. So that's delta. And there's another sine theta here so I'm just going to square that sine theta there. So now the P's cancel out. The b's are going to cancel out. The 12s are going to cancel out. And I'm going to rearrange this a little bit. So I'm going to write Young's modulus of the solid out in the front. Then I've got a term here of t cubed and I'm going to multiply that by 1/l squared, and then everything else-- well, let's see. We can take this l cubed here. I can take that. Put it underneath that, so that's going to give me t/l cubed.
And then I've got an h plus l sine theta here, and I've got an l there, so I'm going to take that to be h/l plus sine theta. Boop-boop-da-doop. So I've got this term with [? h/l's ?] in the thetas. There's a cos theta from the numerator here. This term here turns into h/l plus sine theta, and then I've got my sine squared thetas down there. And that's my result for the Young's modulus in the one direction. OK? Let's make sure that seems right. It seems good. OK.
So one of the things to notice here is there's three types of parameters that are important. So one is the solid properties. So the Young's modulus of the solid comes into this. So the stiffness of the whole thing depends on the stiffness of whatever it's made from. There's this factor of t/l cubed-- that's directly related to the relative density or the volume fraction of solids. So what this is saying is the relative density goes as t/l, so the Young's modulus depends on the cube of the relative density. So it's very sensitive to the relative density.
And then this factor here really is just a factor that depends on the cell geometry. Remember when we talked about the structure of the honeycomb, we said we could define the cell geometry by the ratio of h/l and theta, OK?
And since we often deal with regular hexagonal honeycombs, I'm just going to write down what this works out to be for regular hexagonal honeycombs. So for a regular hexagonal honeycomb, h/l is 1. All the members have the same length. And theta's 3, and the modulus works out to 4 over root 3 times Es times t/l cubed, OK?
So do you see how we do these things? So all the other properties work in a similar kind of way. You have to say something about what the sort of bulk stress is on the whole thing and relate that to the loads on the members. You have to say something about how the loads are related to deflections, or when we look at the strengths, we're going to look at moments and how the moments are related to failure moments of one sort or another. But it's all just like a little structural analysis, OK? Are we good? You good, Teddy? I thought you were going to put your hand up? No? You're OK? OK.
OK, so the next property we're going to look at is Poisson's ratio. And I'm going to look at it for loading in the one direction. So Poisson's 1 2, say we load uniaxially in the one direction, we want to know what the strain is in the two direction, it's minus epsilon 2 over epsilon 1.
And again, if I look at my inclined member, and I say that member's going to bend something like that, and that's my deflection delta there, and, say, got the same x1 and x2 axes. And again, if I look at delta here, it's the same little sketch I had before. That's delta sine theta. And this is delta cos theta. I'm going to need those components to get the two strains in the different directions.
So epsilon 1 is going to be delta sine theta over l cos theta. And if I'm compressing it, that would get shorter. And we get-- and epsilon 2 is going to be delta cos theta divided by h plus l sine theta. And that would get longer. So these two have opposite signs, and so the minus sign is going to disappear here. Doodle-doodle-doot.
So then I can get my Poisson's ratio by just taking the ratio of those two guys. So I could put a minus sign there and say that's the opposite sign to epsilon 2. Then this would be delta cos theta divided by h plus l sine theta. And epsilon 1 would be delta sine theta over l cos theta. And the thing that's convenient here is that the two deltas just cancel out.
So the Poisson's ratio is the ratio of two strains. Each one of the strains is going to be proportional to delta, and so the two deltas are just going to cancel out. And so I can rewrite this thing here as cos squared theta divided by h/l plus sine theta times sine theta.
And so one of the interesting things to notice that the Poisson's ratio only depends on the cell geometry. It doesn't depend on what solid the material is made from. It doesn't depend on the relative density. It only depends on the cell geometry.
Oops.
OK, and then we can also work out what the value is for a regular hexagonal cell. And if we plug-in h is equal to l and theta's equal to 30, you get that it's equal to 1. So one is kind of an unusual number for a Poisson's ratio. When we think of most materials, it's around 0.3, so it's kind of unusual that it's that large.
The other thing that's interesting is that it can be negative. So if theta is less than 0, then you can get a negative value. If the cos squared is going to be a positive value, but you've got a sine theta down here, then that's going to give you a negative value. So you can get negative values. So let me just plug in an example. So say h/l is equal to 2, and theta is equal to minus 30 degrees, then this turns out to be 3/4. So cos of 30 is root 3/2, so square of that is 3/4. h/l is 2, sine theta is 1/2, but it's minus 1/2. So 2 minus 1/2 is 1 and 1/2. And then the sine theta is minus 1/2. And so it works out to be minus 1 for that particular combination.
And I brought my little honeycomb that has a negative Poisson's ratio in. So this guy here-- let's see, I don't think there's an overhead here. No overhead? Guess not. I'll just pass it around. So if you take it, put your hands on the flat side and load it like this, and don't smoosh it like that. Just load it a little bit, because you [? want to be ?] linear elastic. If you load it just a little bit, you can see that as you push it this way, it contracts in sideways that way. So don't smash it. Just load it a little bit and you can kind of see it with your hands. And if you put on a piece of lined paper, it's easier to see it.
OK, so that's kind of interesting. So are we good with getting the Young's modulus in the one direction and the Poisson's ratio for loading in one direction? OK, so you can do the same sort of thing to get the Young's modulus in the two direction and the Poisson's ratio for loading in the two direction. And you get slightly different formulas, but it's the same idea. And you can also get a shear modulus this way, and in-plane shear modulus. It's a little bit-- the geometry of it's a little bit more complicated.
So all of those things are derived in the book, in the cellular solids book. So if you wanted to figure those out, look at that, you could look at the book. So let me just comment on that. All right, so those are the in-plane linear elastic moduli, and remember we said that four of them describe the in-plane properties for an anisotropic honeycomb. And you can use that reciprocal relationship to relate the two Young's moduli and the two Poisson's ratios.
All right, so the next thing I wanted to talk about was the compressive strength. So let me just back up here a second. So if we go back to here, remember we had for an elastomeric honeycomb, this stress plateau was related to elastic buckling. So we're going to look at that buckling stress first. And this plateau here is related to yielding. And then we'll look at the yielding stress next. And then this plateau here is related to a brittle sort of crushing, and we'll do that one third.
So we're going to go through each of those next. And this is kind of a schematic for the elastic buckling. So when you look at the elastic buckling, one of the things to note is that when you load the honeycomb this way on, if you load it in the one direction, you don't get buckling. It just sort of continues to-- whoops, if I can keep it in plane. It all just kind of folds up, so you just get larger and larger bending deflections. You don't really get buckling.
But when you load it this way on, these vertical members here, the ones of length h, they're going to buckle. So, see if I do that, my honeycomb looks like those cells up on the schematic there, OK? So, whoops.
So we're going to look at the compressive stress or strength next. That's sometimes called the plateau stress. So we can get cell collapse by elastic buckling, if, for instance, the honeycomb is made of a polymer. And then the stress-strain curve looks something like that. And what happens is you get buckling of those vertical struts throughout the honeycomb
And then you could also get a stress plateau by plastic yielding. And what happens when you get plastic yielding is you get localization of the deformation. So one band of cells will begin to yield initially, and then as the deformation proceeds, that deformation ban will propagate and get bigger and bigger, and you get a wider and wider band of cells yielding and failing.
So you get localization of yield, and then as deformation progresses, the deformation band widens throughout the material. So if I go back and look-- if I look at this one here, when you look at this middle picture here, you can see how one band of cells has started to collapse and started to fail. And as you continue to compress that in the one direction, this way on, then more and more neighboring cells are going to collapse and the whole thing will get wider until the whole thing has collapsed. And that's kind of characteristic of the plastic failure.
And then the third possibility is brittle crushing. And then you get these kind of serrated plateau. And the peaks and valleys correspond to fractures of individual cell walls.
OK, so we're going to start off with the elastic buckling failure. And I'm going to call these plateau stresses sigma star, for the sort of compressive strength. And el means it's by elastic buckling. And as I mentioned, you don't get it in the one direction. The cells just fold up. You only get it for loading in the two direction, so it's going to be sigma star el 2. Oops, need a different piece of chalk.
So you get this elastic buckling for loading in the x2 direction, and the cell walls of length h buckle. And you don't get it for loading in the one direction, the cells just fold up. So again, let me draw a little kind of unit cell here. And here is our stress sigma 2, like that. And here's our little wall of length h that's going to buckle.
So if I load it up, initially it'll be linear elastic. And then eventually, at some stress, it will get large enough that this wall here will buckle. And we can relate to that plateau stress, or that compressive stress, to some Euler buckling load. So you remember, if we have a pin-ended column, so just a single column, pins on either end, the Euler buckling load says you get buckling when the critical load is equal to some end constraint factor, n squared. So n squared pi squared E, and here it's E of the solid, I over the length of the column, and in this case, the column length is h-- so h squared. OK, so that's just the Euler formula.
And here, n is an end constraint factor. And if you remember for a pin column, so if our column is pinned at both ends like that, and just buckles out like that, then n is equal to 1. And if the column is fixed at both ends, something like that, then the column looks like that and then it's equal to 2, OK? So if I know what the end condition is, I know what n is and I can use my Euler formula here.
So the trick to this is that it's not so obvious what n is. Yes?
AUDIENCE: So, when you're loading in the x2 direction here, the first thing you're going to get is the incline members deforming?
LORNA GIBSON: Yeah.
AUDIENCE: And then at some point, you hit a P critical that will cause the vertical members to buckle?
LORNA GIBSON: Exactly.
AUDIENCE: OK.
LORNA GIBSON: Exactly. That's exactly right. Hello. So the trick here is that we don't really know what this n is, initially. They're not really pinned, pinned; they're not fixed, fixed. And if you think about the setup with the honeycomb here, the constraint on that vertical member depends on how stiff the adjacent members are.
So you can kind of imagine, if I'm looking at one of these vertical members here, if these two adjacent inclined members were big honking thick things, it would be more constrained. And if they were little thin, kind of teeny little membranes, it would be less constrained. And you can think of it in terms of a rotational stiffness, that when the honeycomb buckles, you kind of see the member h goes from being horizontal to sort of it buckles over like this.
But that whole end joint, see the end joint at the top here or the end joint at the bottom, that whole joint rotates a little bit. And so there's some rotational stiffness of that joint. And that rotational stiffness depends on how stiff the member h is and how stiff those inclined members are.
So there's a thing called the elastic line analysis that you can use to calculate what n is. And basically what that does is it matches the rotational stiffness of the column h with the rotational stiffness of those inclined members. So we're not going to get into that. I'm just going to tell you what the answer is. But if you want to go through it, it's in an appendix in the book. So you can look at it, if you want.
So here I'm just going to say that the constraint n depends on the stiffness of the adjacent inclined members.
And we can find that by something called the elastic line analysis. And if you have the book, you can look in the appendix and see how that works. But essentially what it does is it matches the rotational stiffness of the column h with the rotational stiffness of the inclined members.
So what you find is that n depends on the ratio of h/l. And I'm just going to give you a table with a few values. So for h/l equal to 1, then n is equal to 0.686. For h equal to 1.5, it's equal to 0.76. And for h/l equal to 2, it's equal to 0.806.
OK, so now if we have values for n, we can just substitute in to get the critical buckling load. And if I take that load and divide it by the area of the unit cell, I'm going to get my buckling stress. So it's pretty straightforward from this.
So my buckling stress is going to be that critical load divided by my unit cell area. So it's divided by the unit cell length in the x1 direction to l cos theta times the depth b into the page.
So it's equal to n squared pi squared Es times I. And I is bt cubed over 12. Divided by the length of the column, h squared, and then divided by the area of the unit cell, 2l cos theta b, OK? And I can rearrange that somewhat to put it in terms of dimensionless groups.
So if I pull all the constants out, it's n squared pi squared over 24 times the modulus of the solid, t/l cubed in the numerator divided by h/l squared times cos theta in the denominator. So again, you can see that the buckling stress, the compressive sort of elastic collapse stress, depends on the solid property. So here is the modulus of the cell wall in here. Depends on the relative density through t/l cubed. And then it depends on the cell geometry through h/l cos theta, and n depends on h/l as well, OK?
And then we can do the same thing where we figure out what it is for regular hexagonal cells. And it's 0.22 Es times t/l cubed. And then we can also notice that since E in the 2 direction, for a regular hexagonal cell, E is the same in the 2 direction and the 1 direction. It's isotropic. So E2 is also equal to 4 over root 3 Es times t/l cubed. That's equal to-- whoops-- it's equals to 2.31 Es t/l cubed. And we can say that the strain at which that buckling happens is just equal to a constant. And for regular hexagonal honeycombs, it works out to a strain of 10%.
Are we good? So we have a buckling load. We divide by the area. The only complicated thing is finding n. And you can find it by this elastic line analysis thing. So each of these calculations is like a little structural analysis, only on a little teeny weeny scale of the cells. So you see where my background in civil engineering comes in handy. Yup. OK.
So the honeycombs involve the most sort of complicated equations. When we come to do the foams, we're going to use a dimensional analysis and all the equations are going to be much simpler. So this is the most kind of tedious part of the whole thing.
So the next property I want to look at is the plastic collapse stress. Say we had a metal honeycomb and we wanted to calculate the stress plateau for a metal honeycomb. So we have this little schematic here, and say we load it in the one direction again. So we're loading it here. And we've got some load P, like that. And if we have our honeycomb, we load it this way on, initially, the cell walls bend. And you have linear elasticity and you have some Young's modulus.
But if you have a metal, if you continue to deform it and you continue to load it more and more, eventually you're going to hit the yield stress and the cell wall. So the stresses in the cell wall are going to hit the yield stress. And initially, the stresses are just going to be-- remember, if you have a beam, the stresses are maximum at the top and the bottom of the beam. So initially you're going to hit the yield stress at the top and the bottom of the beam first. But as you continue to load it, you're going to end up yielding the cross-section through the entire section. So the entire section is going to be yielded.
And once the entire section yields, it forms what's called a plastic hinge. Once the whole thing's yielded, then you can add more force and the thing just rotates. And because it rotates, it's called a plastic hinge. You know, if you take a coat hanger, and you bend it back and forth and bend it back and forth. If you bend it enough, you form a plastic hinge because it just can bend easily.
So these little schematics here, if you look at the, say, one of these inclined members, the moments are maximum at the end. So Remember when we had the linear elastic deformation and I looked at the little bending moment diagram? The moments are maximum at the ends, and you're going to form those plastic hinges initially at the ends. And so these little ellipsey things here, all the ends, those kind of show where the plastic hinges are. So those plastic hinges are forming. So here's for loading in the x1 direction, and here's for loading in the x2 direction, there.
So the thing we want to calculate is what stress does it take to form those plastic hinges and get this kind of plastic plateau stress?
OK, so we can say we get failure by yielding in the cell walls. And I'm going to say the yield strength of the cell wall is sigma ys. So sigma y for yield and s for the solid. And the plastic hinge forms when the cross-section has fully yielded.
So let's look at the stress distribution through the cross-section when its first linear elastic. So say that's the thickness t of the member. And if the beam was linear elastic, the stress would just [? vary ?] linearly, like that, right? And this would be the neutral axis, here, where there is no normal stress. So that's what happens if it's linear elastic, and I'm hoping you remember something vaguely like that. Sounds good?
But as we increase the load on it, and we increase the sort of external stress, this stress in the member is going to get bigger and bigger, and eventually, that's going to reach the yield stress, OK? And once that reaches the yield stress, if we continue to load it, what happens is the yielding propagates down through the thickness of the thing here. So we get yielding through the whole cross-section. So let me scoot over here.
AUDIENCE: Professor?
LORNA GIBSON: Yup?
AUDIENCE: When it starts to yield, does this curve change?
LORNA GIBSON: Yes. I'm going to draw it for you.
AUDIENCE: Oh, OK.
LORNA GIBSON: That's the next step. That would be the next thing.
OK, so once the stress at the outer fiber is the yield strength of the solid, then the yielding begins and it progresses through the section as the load increases.
So the stress distribution starts to look something like this once it yields. OK, so that's sigma y of the solid. Actually, let me rub that out because then I can show you something else. So in 3D, this would be through the thickness of the beam. That would be the thickness of the beam there. And boop, boop. It would look something like that. OK? And then this is still our neutral axis here.
And then eventually, as you load it more and more, the whole cross-section is going to yield. Whoops.
And I'm assuming that the material is elastic, perfectly plastic.
So the stress-strain curve from the solid I'm idealizing as-- whoops. That's not quite right. I'm idealizing as that, OK? So when you get to this point here, the entire cross-section has yielded, and that means you form the plastic hinge.
The idea here is that the section then just rotates like a pin.
All right.
So we can figure out the plateau stress that corresponds to this by looking at the moment that's associated with the plastic hinge formation. So there's some internal moment associated with that. And then equating that to the applied moment from the applied stress. So doodle-loodle-oot. Let me see me, maybe back up here.
So there's some-- if I have the stress distribution here, I could say this whole kind of stress block is equivalent to some force acting out like that and some force acting out like that. It would be sigma ys times b comes t/2 would be f. And I can say there's some plastic moment. If I think of the force here and the force there, they act as a couple and they have some moment, and that's called the plastic moment. So that's like an internal moment when the plastic hinge forms.
So I'll say the internal moment at the formation of a plastic hinge. I'm going to call that Mp, for plastic moment. And we can work out Mp by looking at that stress distribution when the entire cross section has yielded. The force F is going to be sigma ys times b comes t/2. It's the stress times that area. And then the moment arm between the two forces is also t/2. And so that plastic moment is just sigma ys bt squared over 4, OK? Are we good? Sonya?
AUDIENCE: What's the second [INAUDIBLE]?
LORNA GIBSON: OK, so this is the force. This thing here is the force F. And I have to-- if I'm getting a moment, I'm saying that that force, if I doot-doot-doot-- the distance between those two forces there is t/2. So each force acts through the middle of the block, and so the distance between [? it is ?] t/2.
And I'm going to equate that moment to the applied moment from the sort of applied stress. And then if I go back to my inclined member-- whoops, let's see. Let me get a little more inclined. That's my inclined member, there, of length l. I've got modes p that are applied at the end from sigma 1. And I've got moments that are induced at the ends.
And that angle there would be theta. This length here is l, like that. And if I just use static equilibrium on that, I can say that I've got 2 times the moment, so I've got one at each end-- they're both the same sign-- minus P. And then the distance between these two P's, say I take moments about here, I've got M applied plus M applied, I've got minus P times l sine theta. That's equal to 0.
So the applied moment there is just Pl sine theta over 2. So now what I'm going to do is I'm going to equate this applied moment with this plastic moment, and I'm going to relate P to my applied stress sigma 1. And then I'm going to get a strength in terms of the yield strength of the solid, there's going to be a t/l factor and there's going to be some geometrical factor. So that's just the last step. Boop-ba-doop-ba-doop.
So we get plastic collapse of the honeycomb. And the stress I'm going to call sigma star plastic with a 1, because I'm going to look at the one direction. And that happens when that internal plastic moment equals the applied moment.
So let's see. I've got that. Let me also write down over here, I've also got this sigma 1 is equal to P over h plus l sine theta times b. So here I can write P in terms of sigma 1, in this thing. And then write that, get the applied moment in terms of that, and then equate it to that.
So this term on the left-hand side corresponds to this expression for the applied moment where I've plugged in. For P, I've plugged in sigma 1 times h plus l sine theta times b. And that's my plastic moment on the right-hand side. So if I just rearrange this, I can then solve for this plastic collapse stress. So it's equal to the yield strength of the solid times t/l squared, and then times another geometrical factor. 2 times h/l plus sine theta times sine theta. Doop-doop-doop.
So the same kind of thing, there's a solid property, a t/l, a relative density term, in then a cell geometry term. And we can calculate with this for regular hexagonal cells.
And we can do a similar kind of calculation for loading in the other direction.
And you can get a shear strength if you want to do that, too.
AUDIENCE: If you're going in the other direction, only the E or the M apply changes, right? [? Or ?] like that section.
LORNA GIBSON: Yeah, this thing here is the same.
AUDIENCE: That stays.
LORNA GIBSON: Right. And this is-- there's a different geometry to it. Because now you're loading it this way on.
OK, so we've calculated an elastic buckling plateau stress and a sort of plastic collapse plateau stress. And if you have thin enough walled, say, even aluminum honeycombs, then the elastic buckling could precede the plastic collapse. And so I'm just going to work out what the criterion would be for that to happen.
So the two stresses can be equated. And then that's going to give us some criterion. So the two are equal, I'm just going to write down the equations that we had. So the buckling stress was n squared pi squared over 24 times E of the solid times t/l cubed divided by h/l squared times cos of theta. And the plastic collapse stress for the 2 direction was sigma ys times t/l squared divided by 2 cos squared theta.
So I can write this-- because this has a t/l cubed term, and that has a t/l squared term, I can write this in terms of a t/l critical. So if I leave it t/l here and I put everything else on the other side, I've got 12 over n squared pi squared, then h/l squared over cos theta times sigma ys over Es.
So if t/l is less than that, I'm going to get elastic buckling first. And if it's more than that, I'm going to get plastic yielding first. And we can work out an exact number for regular hexagonal honeycombs, so I'm going to do that. So if I have a particular geometry, I can figure out what n is. So for regular hexagonal honeycombs, t/l critical just works out to 3 times the yield strength of the solid over the Young's modulus of the solid.
So if we know that ratio of the yield strength of the modulus of the solid, we can get some idea of what that critical t/l would be. So we'll do that next.
AUDIENCE: And you said if t/l is less than that critical, then you're going to get the yielding first.
LORNA GIBSON: No, if it's less, you get the buckling first. If it's really skinny, it tends to buckle first.
So, for example, for metals, the yield strength over the modulus is roughly 0.002, like the 0.2% yield strength. And so that means that t/l, the sort of transition or the critical value is at 0.6%. So most metal honeycombs are denser than that. That's a pretty low density.
But if we look at polymers, you can get polymers with a yield strength relative to the modulus of about 3% to 5%, and then that critical t/l is equal to about 10%, 15%. So low-density polymers with yield points may buckle before they yield.
So we have one more of these compressive plateau stresses, and that's for the brittle honeycomb. So I don't think I'm going to finish this today, but let me set it up and then we'll finish it next time.
So the idea here is that if you have a ceramic honeycomb-- remember I showed you some of those ceramic honeycombs-- that if you compress them, they can fail by a brittle crushing mode. So ceramic honeycombs can fail in a brittle manner.
And again, initially there would be some cell wall bending, but at some point, you're going to reach the bending strength of the material. And bending strengths are called modulus of rupture. So you reach the modulus of rupture of the cell wall.
So I'm not going to write the equations down today because we're not going to get very far, so I'll do that next time. But we're going to set this up exactly the same as we did for the last one, for the plastic yielding. But instead of getting that sort of blocky, fully yielded cross-section stress distribution, we're just going to have the linear elastic stress distribution, and when the maximum stress reaches that modulus [? rupture, ?] the thing's going to fail.
So the form of the equations is going to be very similar to what we had for the plastic collapse stress, but there's a slightly different geometrical factor-- that's all. So we'll do that next time. And then next time we're also going to talk about the tensile behavior of honeycombs in-plane. We'll work out a fracture toughness and then we'll start talking about the out-of-plane properties, as well. So on Wednesday, we'll do the out-of-plane properties, OK?
So hopefully we'll finish the out-of-plane properties Wednesday. And then next week, I was going to talk about some natural materials that have honeycomb-like structures, so things like wood and cork, OK? All right, so this is the kind of most equationy lecture in the whole course.
Free Downloads
Video
- iTunes U (MP4 - 170MB)
- Internet Archive (MP4 - 170MB)
Subtitle
- English - US (SRT)